What is Preventive Maintenance?
Preventive Maintenance (PM) is used to strategically maintain, repair, or replace equipment before an uncertainty occurs, with the aim of improving the uptime of heavy equipment and machinery.
Effective Preventive Maintenance is planned and scheduled using real-time data insights. Since maintaining a Preventive Maintenance schedule for a large amount of equipment is challenging, many businesses often use software such as a CMMS. To avoid unexpected breakdowns, preventive maintenance is performed while the equipment is functioning.
Preventive Maintenance is the exact opposite of Deferred Maintenance, whereby managers tend to postpone maintenance and repairs to a later date due to the lack of resources and to save money or meet funding levels.
Why do you need a Preventive Maintenance plan?
“A successful maintenance strategy usually requires the planning and scheduling of equipment maintenance prior to the occurrence of an issue”.
A Preventive Maintenance plan is a set of processes, guidelines and tools required for carrying out maintenance checks on a regular basis. This helps keep the facilities in working condition and avoids downtime due to failures or breakdowns.
Planned Preventive Maintenance, sometimes referred to as Scheduled Maintenance also includes keeping records of past inspections and equipment servicing.
When do you plan Preventive Maintenance?
Preventive Maintenance includes both planning as well as scheduling the maintenance. While the plan addresses what needs to be done and how; scheduling addresses who will perform it and when.
Property Managers can plan Preventive Maintenance based on a number of factors. Using time-based and interval-based maintenance techniques, simple Preventive Maintenance tasks can be planned in advance. For tasks that are fairly complex in nature, a combination of time-based, interval-based, and condition monitoring Preventive Maintenance activities can be used.
Preventive Maintenance can also be planned based on failure finding, following a risk analysis, prescriptive maintenance or predictive maintenance.
Advantages of Preventive Maintenance
For businesses that rely on their assets for revenue, the process of scheduling routinely planned maintenance is critical. As a result, most businesses that are relying on their assets prefer preventive maintenance over other strategies such as reactive maintenance.
Preventive Maintenance provides several advantages to businesses including;
#1. Prolonged Equipment Lifespan
#2. Reduced Risk of Injury and Improved Safety
#3. Cost Reduction
#4. Increase in Productivity
#5. Reduction in Energy Consumption
“Preventive Maintenance can also be beneficial to the environment because poorly maintained electrical assets consume more energy than those that are properly maintained”.
Of course, there is also the financial benefit of reduced electricity bills.
When you run regular preventive maintenance on your HVAC system, it consumes less amount of energy for heating and cooling the building and hence costs less to run.
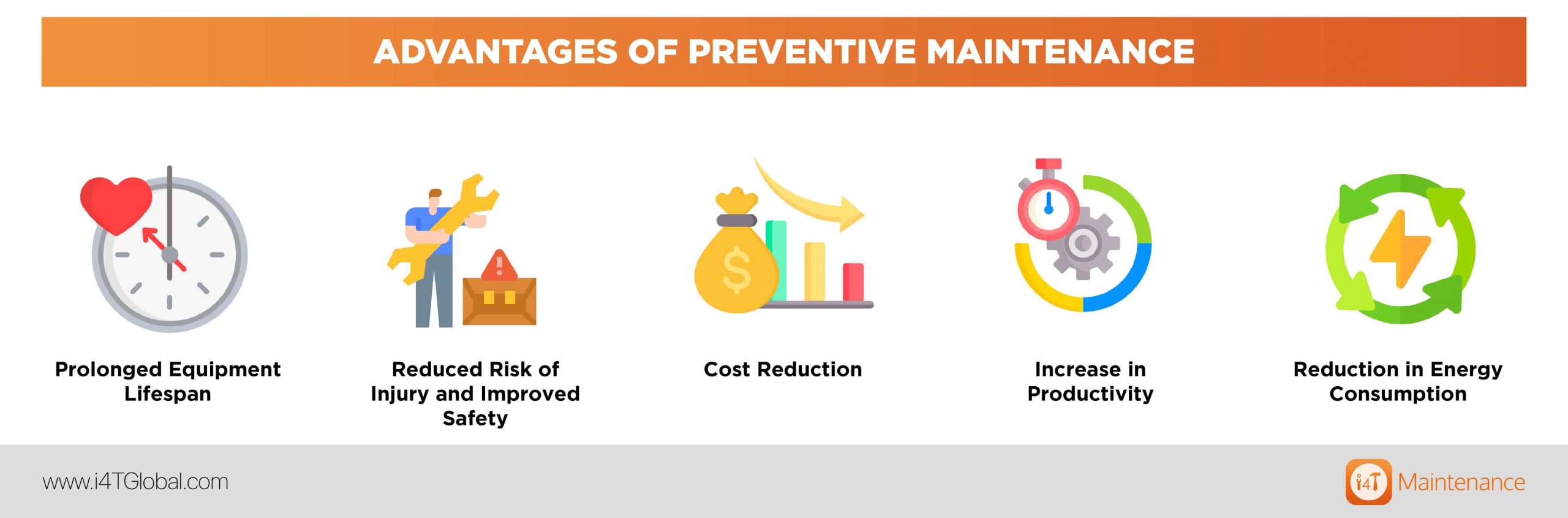
Disadvantages of Preventive Maintenance
Upfront Costs
Labour-Intensive
Budget is not the only thing that needs to be set aside. You will require more staff to carry out all the steps required for Preventative Maintenance. This means that the staff are spending more time on preventative maintenance, when they could be doing other work. It could also mean more personnel needed to be hired and paid for the same. These personnel include plant managers, supervisors and operators. You might also need to take into account vendor management to hire and manage technicians carrying out specific maintenance tasks.
Chances of Over-Maintenance
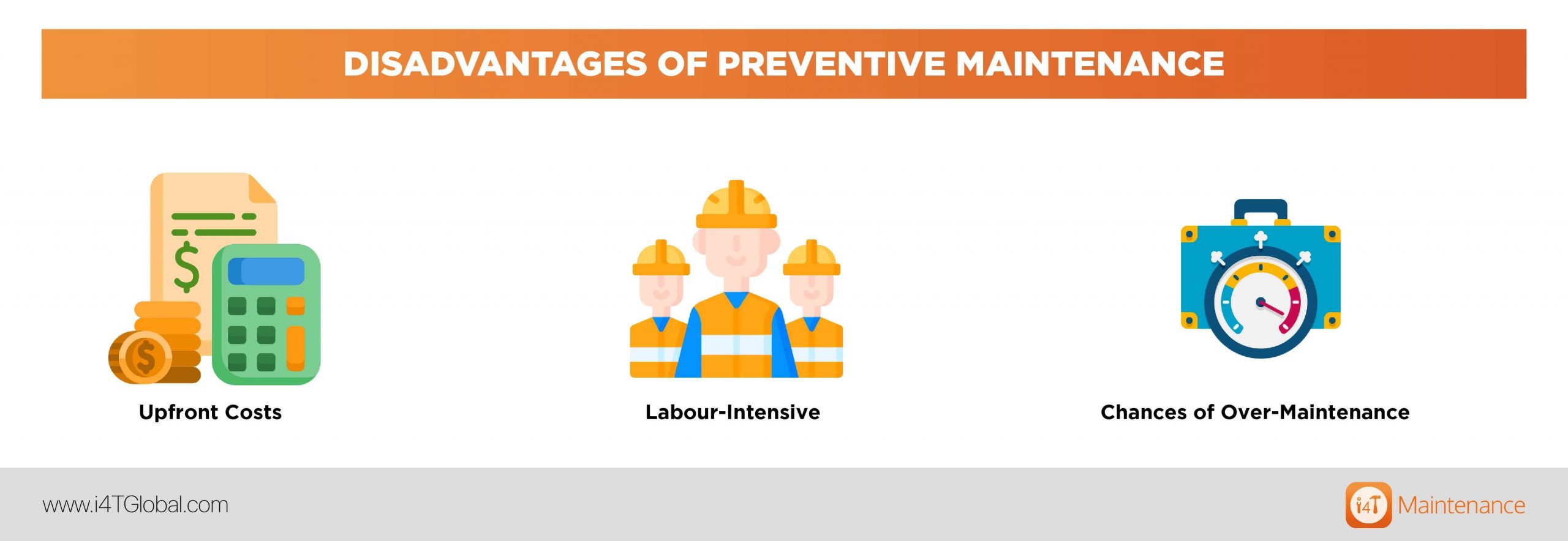
Types of Preventive Maintenance
Preventive maintenance is classified into the following types:
- Predictive maintenance
- Prescriptive maintenance
- Failure-finding maintenance
- Risk-based maintenance
- Time-based maintenance
- Usage based maintenance
- Condition based maintenance
To avoid unplanned failure, a variation of these types of preventive maintenance should ideally be scheduled and performed on all items of equipment. Manufacturers frequently provide recommendations on how to best maintain their equipment.
Your maintenance team can schedule preventive maintenance using the appropriate type of preventive maintenance in addition to real-time data insights. Examples of each type of preventive maintenance are provided below.
#1. Predictive maintenance
#2. Prescriptive maintenance
#3. Failure-finding maintenance
#4. Risk-based maintenance
#5. Time-Based Preventive Maintenance
#6. Usage-Based Preventive Maintenance
#7. Condition-Based Preventive Maintenance
Finding the best preventive maintenance type for you
Now that you understand what the different types of preventative maintenance are, it’s time to decide which one best fits a given scenario.
The main factors that you need to consider here are:
- Cost of asset failure: To determine this cost you need to ask yourself what will be the impact in case the equipment breakdown. These impacts can range from equipment downtime, repair costs, employee safety and environmental impact. If you know why the equipment fails, it would be easier to develop a plan to prevent it.
- Ease of monitoring the asset: This factor considers the cost of monitoring the equipment compared to the cost of letting it fail. If the monitoring cost is more, the strategy is not worth implementing.
Based on these two factors, you can now put together a team, analyse how much it will cost you if the asset fails, rank your strategies based on highest to lowest cost of monitoring for each asset, and finally choose a maintenance strategy based on this.
The Preventive Maintenance Workflow
Setting up a preventive maintenance schedule for your major equipment ensures that your facilities are functioning efficiently and productively.
A typical preventive maintenance workflow is depicted in the flowchart below. Your organisation may choose to add, remove, or adjust steps as needed to fit your specific processes. A preventive maintenance workflow typically includes the following action items.
- Inspection
- Detection
- Correction
- Prevention
Industrial Benefits from Preventive Maintenance
#1. Security
#2. Quality
#3. Cost
#4. Availability
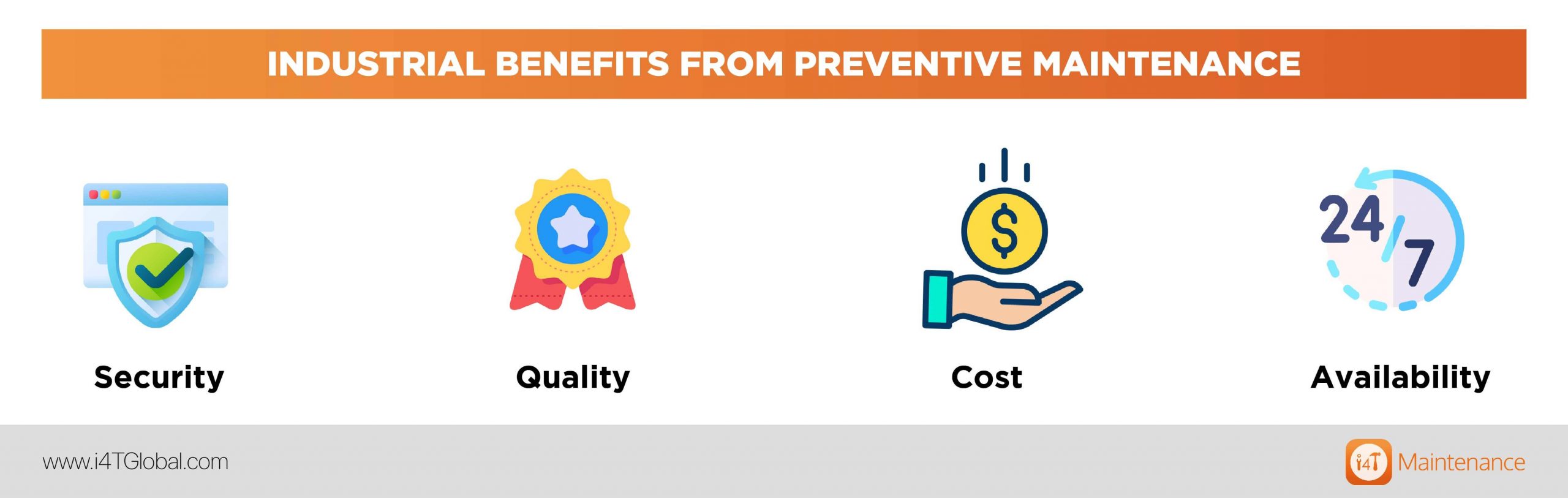
Checklist to create a preventive maintenance plan
A preventive maintenance checklist outlines all the routine and non-routine tasks that technicians need to carry out in a step by step manner to prevent and correct critical issues.
These are created based on the type of asset that needs to be maintained for example, machinery, building or vehicles. While there is no one-size-fits-all checklist, there are certain steps that are common among all.
Step 1: Lay out the objective
You begin with the goal of the preventive maintenance and what you wish to accomplish as a result. Your objective could be to cut down operational costs, minimise downtime, improve compliance or safety.
Step 2: Run an equipment audit
Document the condition of your equipment in detail. Take note of model, serial number, parts replaced in the past, average downtime, time to repair and maintenance costs.
Step 3: Take into consideration standards and regulation
Some maintenance tasks need to be carried out in order to comply with state regulations. When creating your checklist make sure you are adhering to these requirements.
Step 4: Choose assets for maintenance
Prioritise assets that need to be taken care of first, in terms of preventative maintenance. You can categorise your assets based on risk associated with them and the impact it would make if not attended.
Step 5: Make a list of task to be performed for each asset
Think about what preventive maintenance tasks are required for each asset. Make a list and add things like tuning, change over and regular upgrades. Also consider the frequency and priority of each task.
Step 6: Add instructions for each task
Whatever you put on the task list, make sure it is described in full detail so the technician would know exactly what to do and how to do it. Along with these details, mention the time it needs to be completed at.
Step 7: Train your team to use the checklist effectively
Outline best-practices to carry out each task in the checklist to ensure quality of work. Make sure each member of the team is well-versed on how to use the checklist for the intended purpose. If not, provide training where needed.
Step 8: Measure results and adjust checklist items accordingly
Just like any other activity, preventive maintenance checklist also needs to be measured in terms of how useful it has been to achieve your objectives. Over time, you would be able to identify unnecessary items or may find the need to add something more to it. Tracking the results will help you do that.
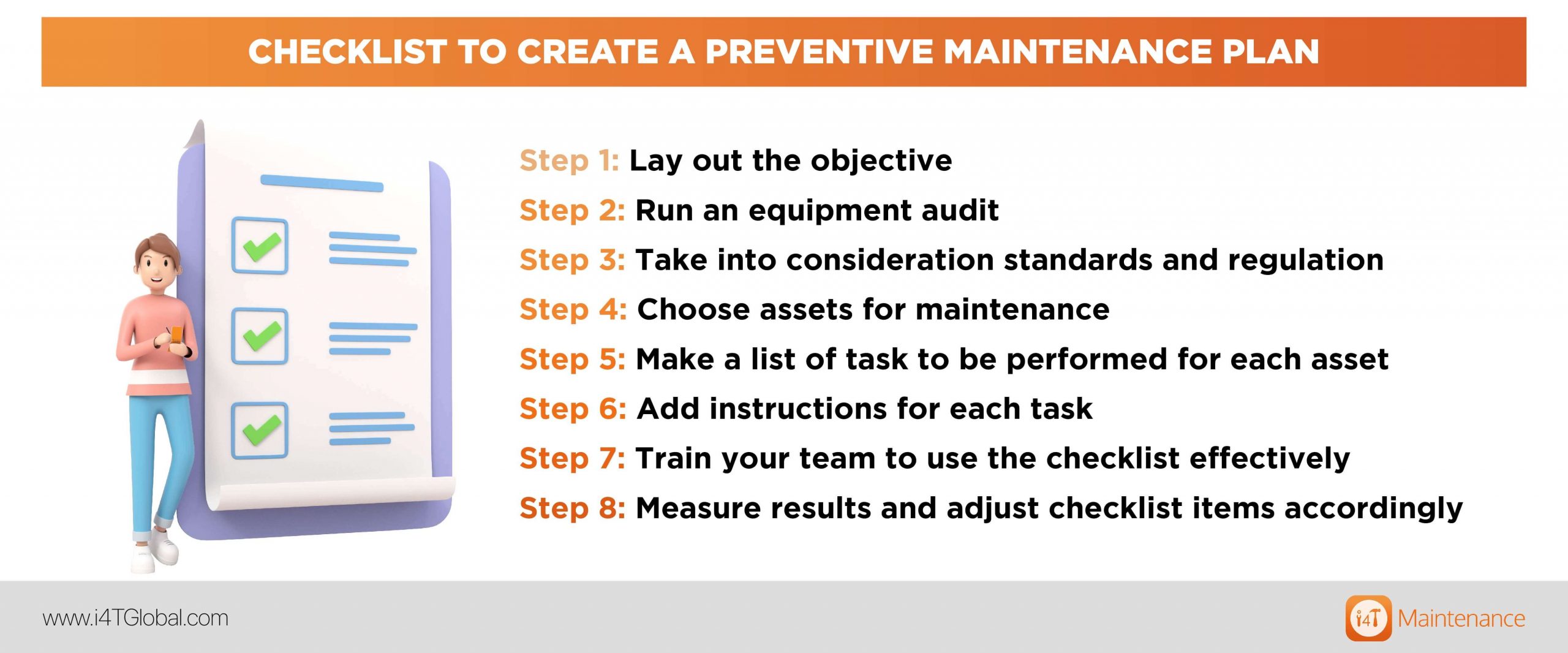
How Can Preventive Maintenance Software Help?
“Many businesses use preventive maintenance software to coordinate all of their preventive maintenance tasks because it simplifies what would otherwise be a complicated process”.
Preventive maintenance software saves a company’s maintenance data on a computer so that all inspections, repairs, and replacements can be easily tracked.
Preventive maintenance software can be used to effectively manage work orders, purchase orders, inventory, and maintenance records because all data is conveniently stored in one location. Preventive maintenance software even prioritises maintenance tasks and collects the information required for maintenance work.
There are several key advantages to using preventive maintenance software.
It helps in managing all maintenance tasks (as well as the records of those tasks) to ensure that maintenance operations run smoothly. It can also save cost on maintenance because the system can plan and prioritise maintenance tasks based on operations.
This minimises disruption to the work schedule when maintenance is performed. Finally, preventive maintenance software relieves technicians of administrative duties, allowing them to focus on their work.
Types of Preventive Maintenance Software
Computerised Maintenance Management Systems (CMMS)
Enterprise Asset Management (EAM)
Enterprise Resource Planning (ERP)
Using a CMMS Software for Preventive Maintenance
Creating recurring preventive maintenance tasks and procedures using a work order and the PM scheduling module.
Accessing PM Information for assets in the field using any electronic device.
Uploading asset documentation, receipts, and proper O&M manuals for future use.
Keeping updated with a data reporting dashboard.
Other Types of Maintenance Strategies
Reactive Maintenance
Predictive Maintenance (PdM)
The practice of gathering analytical data from sensors and IoT devices, storing it in a maintenance management system, and predicting when assets will fail is known as predictive maintenance. Predictions are based on asset condition monitoring, with the goal of identifying maintenance before failure.
PdM analyses data gathered from experts, equipment readers, and previous experience to determine when specific conditions are met. Industry 4.0-based Internet of Things feedback is increasingly being used to inform PdM and help optimise PM requirements.
Bottom Line
Preventive Maintenance (PM) is the regular and routine maintenance of equipment and assets in order to keep them running while preventing costly unplanned downtime due to unexpected equipment failure.
“Preventive maintenance is planned based on usage or time-based triggers. The goal of the PM is to reduce the likelihood of equipment failure”.
In many cases, preventive maintenance is the best maintenance strategy to use. Implementing a PM strategy is much easier with the help of maintenance software, such as CMMS software.
Hot off the press!
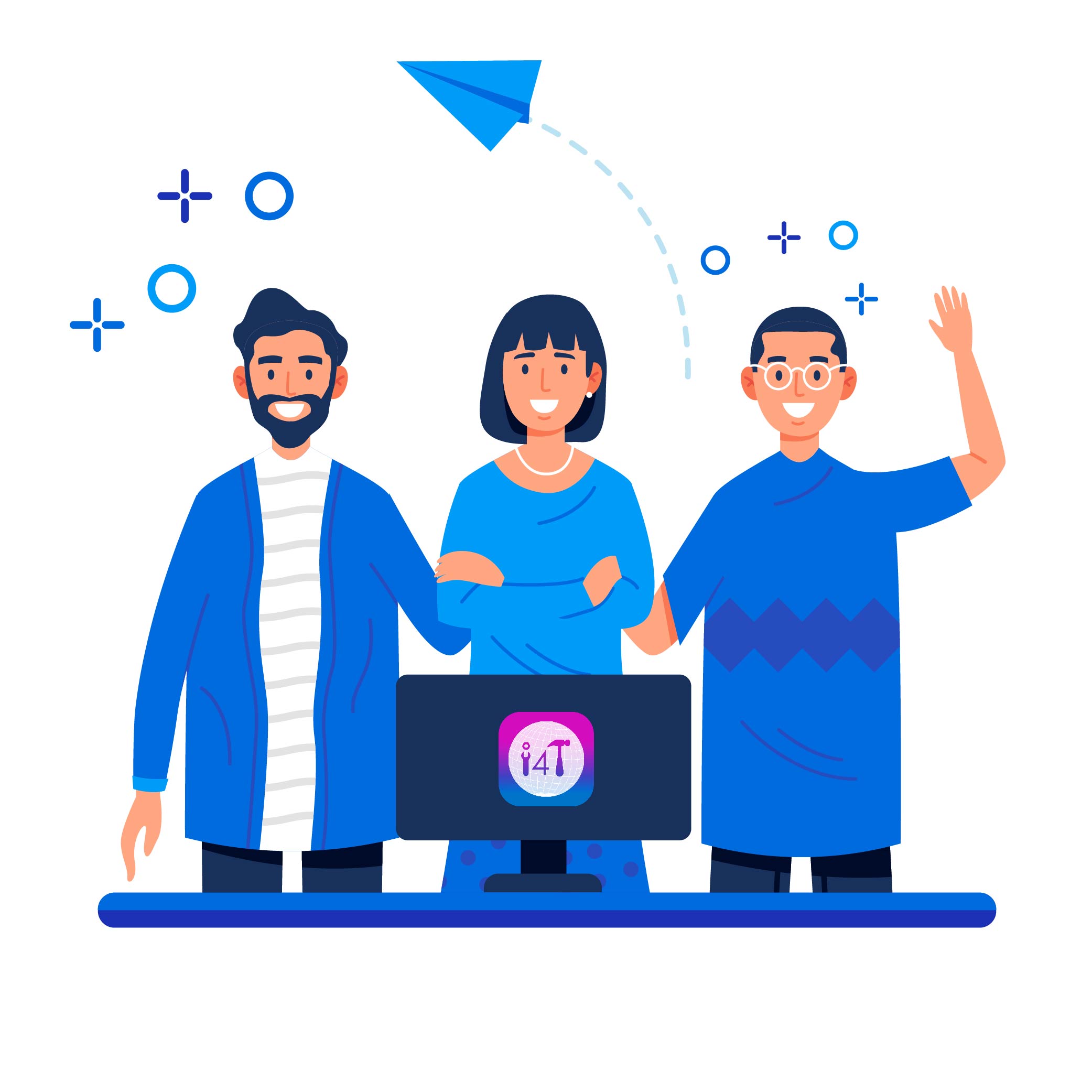
With our cutting-edge technology and in-depth knowledge of how the Field Service Management sector operates, the i4TGlobal Team loves to share industry insights to help streamline your business processes and generate new leads. We are driven by innovation and are passionate about delivering solutions that are transparent, compliant, efficient and safe for all stakeholders and across all touch points.