In Field Service Management, businesses can use various strategies and technologies to move towards proactive and predictive service. It involves:
- Applying statistics and data analysis to predict equipment problems,
- Planning maintenance with AI (Artificial Intelligence) and ML (Machine Learning),
- Using IoT devices to their full potential,
- Investing in cutting-edge technology,
- Giving the team thorough training,
- Improving communication, and
- Updating FSM software.
As a result, companies can make customers happier and more loyal by putting customers’ needs first and giving them customer service.
Use statistics and data
Use the information you already have, like your customers’ past service data and how well your equipment works, to predict problems before they happen. If a piece of equipment usually breaks down after a certain amount of use, plan maintenance before that time.
Here’s how to do it:
- Find out how often and for how long the equipment is used and any other information about the customer. This information can come from customer databases, equipment logs, or devices linked to the internet.
- Next, look at the data you have collected to see if there are any trends. For example, if a machine usually breaks down after being used for a certain duration, you can use that knowledge to guess when it might break down again.
- Use what you’ve learned from the data to set up repair before the equipment breaks down. Planned Maintenance keeps things moving well and keeps equipment from breaking down.
Who should do this:
- Data analysts are people who collect and look at data to find trends. They do this with special statistical tools and methods.
- Service Managers find trends in the data and use them to plan maintenance.
- Technicians need to know why maintenance is scheduled for specific times and stick to the routine.
- IT Professionals help set up and take care of the tools used to gather and process the data. Then, they get the material ready to be looked at.
- Executives use the facts to help them decide what to do. This could be about buying new technology or sending techs to school.
Use planned maintenance
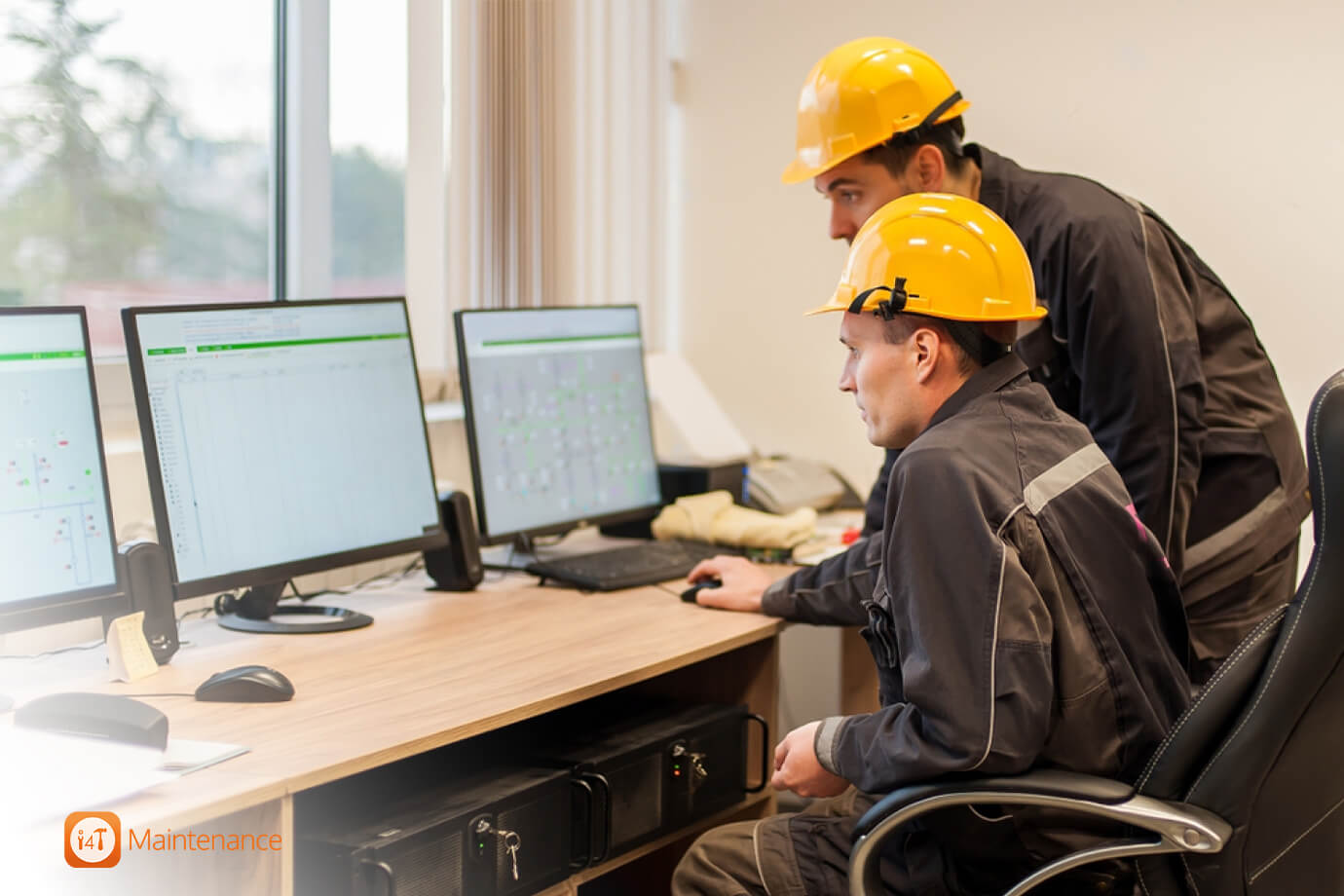
By analysing sensor, operational, and environmental data, you can use AI and machine learning to predict equipment breakdowns before they happen. Then, if a problem looks genuine, the system can plan maintenance to keep it from happening.
Businesses can take better care of their equipment by using tools that predict when it will break down. These systems look at different kinds of data with the help of AI and machine learning. A warning is given when a potential problem is detected. This makes it easier to plan upkeep before something breaks, which saves money and time.
Different people play different roles here:
- IT experts set up and care for the systems that can tell when equipment will break down.
- Data analysts ensure the data is read correctly and the correct problems are found.
- Repair managers decide when to do repairs based on what the system tells them.
- Maintenance technicians do the regular maintenance work.
- Decision-makers know what the system does, give the go-ahead for any spending that needs to be done, and monitor how it makes things more efficient.
Use Internet of Things (IoT) devices
IoT devices can send real-time information about how technology works so that problems can be fixed quickly. They also make checking on equipment from afar possible, reducing the need for site visits.
Businesses can take better care of their equipment by using tools that predict when it will break down. These systems look at different kinds of data with the help of AI and machine learning.
Harnessing the Power of the Internet of Things for Preventive Maintenance:
Using Internet of Things (IoT) devices is vital in transitioning to proactive maintenance. These devices provide real-time information about equipment operation, enabling quick problem resolution and reducing on-site visits.
How it works is as follows:
- IT professionals put IoT devices (sensors) in place that meet specific business needs. These devices gather and send important information about how the equipment works.
- An IoT platform or system connects IoT devices and processes the transmitted data, transforming it into actionable insights.
- The IoT platform has tools for observing and analysing data in real-time. The IoT platform lets companies monitor how their equipment works and spot problems before they worsen.
- Internet of Things (IoT) devices allow businesses to do maintenance chores remotely. This feature reduces downtime, especially for minor problems that don’t need experts on-site.
Key players must actively engage to ensure a successful transition to a proactive maintenance model with IoT.
- IT professionals choose the right Internet of Things devices, add them to the system, and ensure they work.
- Data analysts and scientists keep an eye on IoT data and determine what it means to find possible problems and take preventative steps.
- Maintenance Technicians get information from the IoT tool that helps them do their jobs better.
- Executives and decision-makers understand the benefits of integrating IoT, such as increased efficiency and fewer trips to the site. They decide whether to invest in IoT and drive the change to preventive upkeep. This makes it easier to plan maintenance before something breaks, which saves money and time.
Spend money on new technology
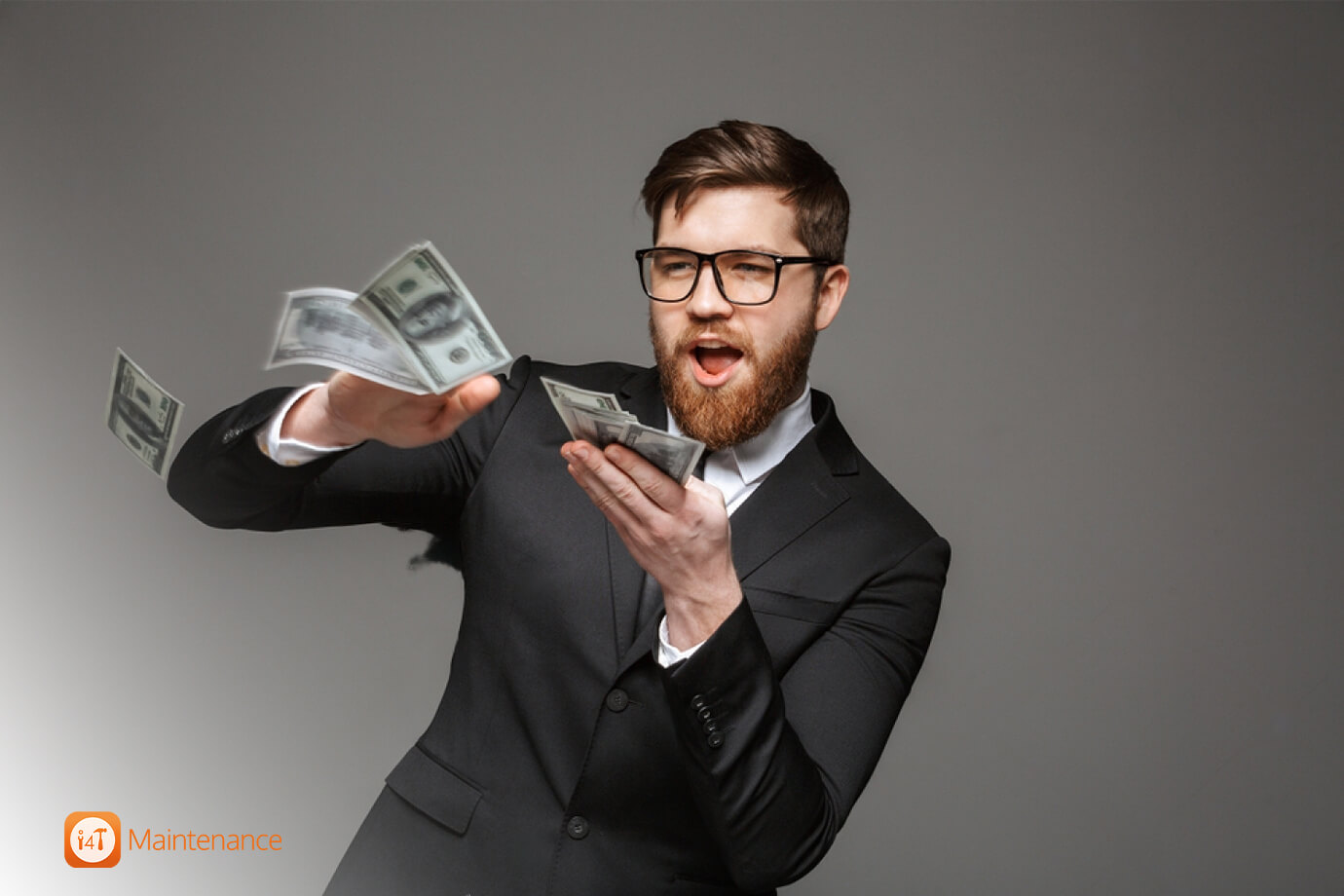
AI, Machine Learning, and Augmented Reality (AR) can help technicians quickly analyse data, predict possible problems, and get help with maintenance chores.
To transition to a proactive maintenance approach using AI, Machine Learning, or AR
- Assess your maintenance needs and identify areas where these technologies can help.
- Research and select suitable solutions that align with your requirements.
- Implement and integrate the chosen technologies with the help of IT professionals or external experts.
- Train your technicians and staff on using the new tools and explain their benefits.
- Establish a support system to address technical issues and continuously improve the implemented solutions.
The successful implementation of new technologies involves various key players.
- IT Professionals assess, select, implement, and integrate new technologies while ensuring smooth connectivity and functionality.
- Maintenance Managers or Supervisors understand maintenance challenges, oversee technology adoption, and ensure proper training and support for technicians.
- Technicians utilise the new technologies in their daily maintenance tasks. Therefore, active participation in training sessions and providing feedback on tool usability are crucial.
- External Consultants or Vendors may offer guidance, support, or specialised training for implementing AI, Machine Learning, or AR solutions, if necessary.
Train your team
Ensure that your employees know how to use these new tools and know how important it is to be proactive.
Think about the following tips for training your team well.
- Customised Training Programmes to meet the goals and roles of each employee. Focus on showing them how to use the new tools and best practices for preventive maintenance.
- Hands-on Practical Training, in which workers can use the tools in real-world situations. Encourage people to take part and find solutions.
- Give your workers regular workshops, webinars, or online courses to keep them up-to-date on proactive maintenance and new technology.
- Inside Information Employees can learn from each other’s experiences, tips, and best practices. To do this, use team meetings, forums, or internal tools.
- Organise group tasks using new tools to get people to work together and as a team.
- Help people share their skills and find solutions to problems. Continuously monitor how your employees are doing and give comments to help them improve their skills and deal with problems.
- Ensure that leadership actively supports proactive upkeep and new tools and lets people know their importance.
Improve communication
Keep everyone in your organisation and your customers updated on the state of your equipment and when it needs to be serviced.
Improving communication within your organisation and with your customers is essential for a successful transition to proactive maintenance.
Here are some strategies to consider:
- Establish a system to update equipment status and upcoming maintenance schedules regularly.
- Implement clear communication channels, such as email, messaging platforms, or project management tools, to facilitate seamless communication among team members and customers.
- Use collaborative platforms where employees can share information, updates, and documents related to maintenance tasks.
- Set up automated notifications to alert relevant parties about upcoming maintenance requirements or changes in equipment status.
- Regularly communicate with customers to update them on the status of their equipment, scheduled maintenance, and any potential issues that may arise.
- Ensure prompt response to customer inquiries or concerns related to maintenance.
- Establish channels for collecting employee and customer feedback regarding the effectiveness of communication processes. This allows for continuous improvement and adaptation to their needs.
Get your software up-to-date
Your Field Service Management software should work with service models that are both predictive and proactive. Look for things like advanced data, automated scheduling, and real-time tracking.
To ensure this, follow these simplified steps:
- Evaluate your current software for compatibility with proactive and predictive service models.
- Research and choose software with advanced data analytics, automated scheduling, and real-time tracking capabilities.
- Engage with software providers to understand their offerings and request demos or trials.
- Assess integration requirements with your existing systems and plan for implementation.
- Migrate data and configure the new software to align with your business processes.
- Provide comprehensive training to your team on using the updated software.
- Establish a support system for addressing technical issues and stay updated with software updates and new features.
Focus on the customer
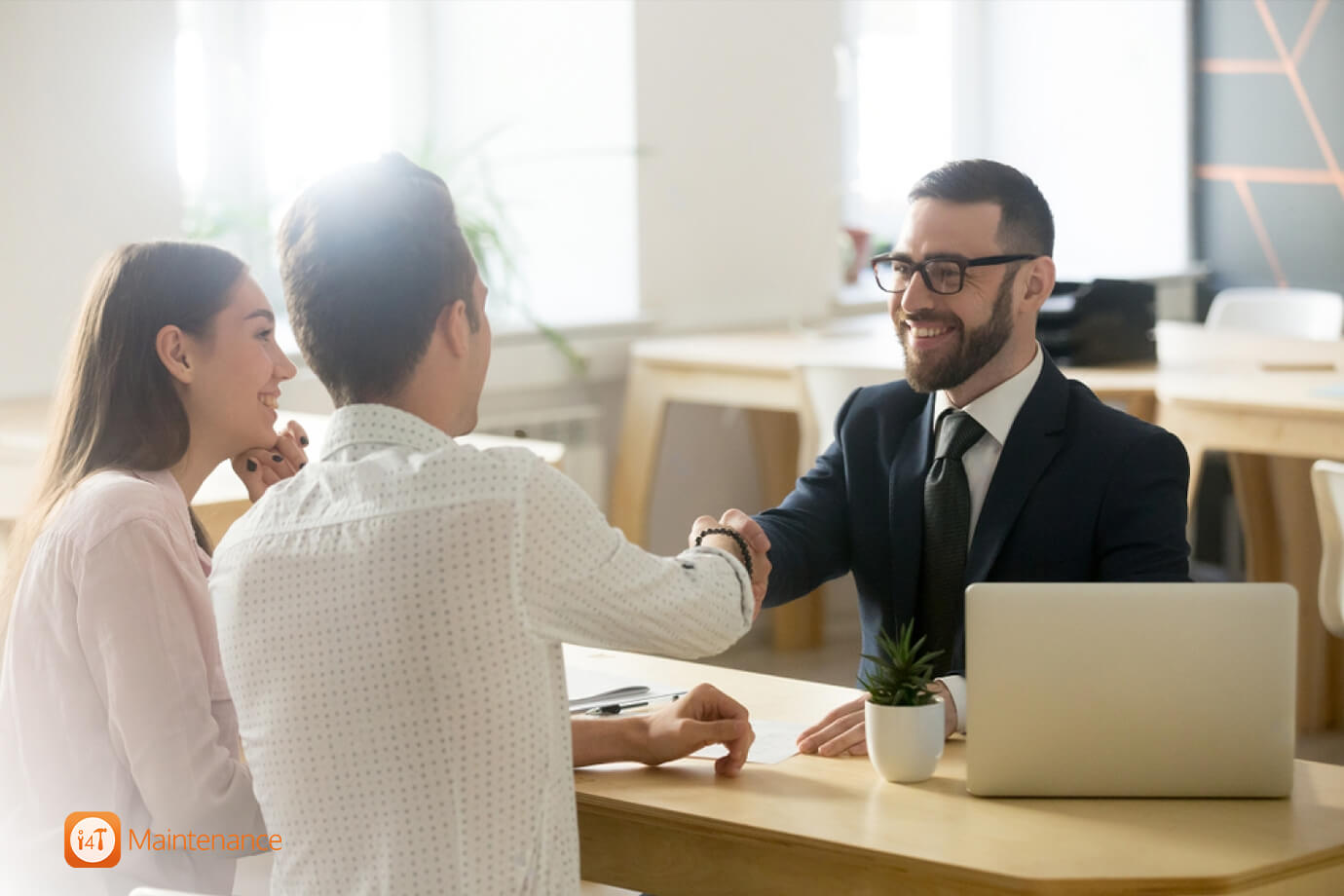
Learn what your people want and need, and make sure your service meets those needs. A proactive service plan should keep equipment from breaking down and improve things for customers.
To put the customer first and make sure your service meets their needs, you need to:
- Research and obtain customer feedback that can help you determine what customers want and need.
- Trace a customer’s path to find places where thoughtful service can add value.
- Use data analysis and real-time tracking to solve problems before they happen.
- Personalise service to meet the needs of each customer.
- Use good communication to keep customers up-to-date and answer their concerns.
- Improve service based on what customers say and how their needs change.
Customer focus can be the job of the customer service team, the product manager, the marketing team, the service technician, and the top leadership.
Putting the customer first and involving different parties can make customers happier and more loyal.
i4T Maintenance is a revolutionary Maintenance Management Software that can help you stay on top of your proactive maintenance goals. Request a Demo.
FAQs
Proactive field service management is an approach that focuses on addressing potential issues before they occur, using data and technology to predict equipment failures and improve service efficiency.
Proactive field service management is an approach that focuses on addressing potential issues before they occur, using data and technology to predict equipment failures and improve service efficiency.
Data analysis helps businesses identify patterns and trends in equipment usage and customer information, allowing them to predict and schedule maintenance proactively, reducing downtime.
IoT devices provide real-time information about equipment operation, enabling businesses to monitor performance, detect issues, and perform timely maintenance or repairs, reducing downtime and improving efficiency.
AI and Machine Learning analyse large amounts of data to predict equipment failures, recommended maintenance schedules, and optimise resource allocation, helping businesses transition to proactive maintenance practices and improve service levels.
Customer focus ensures that services meet customer needs and expectations. By understanding customer requirements, personalising service, and maintaining open communication, businesses can enhance customer satisfaction, build loyalty, and stand out from competitors.
Hot off the press!
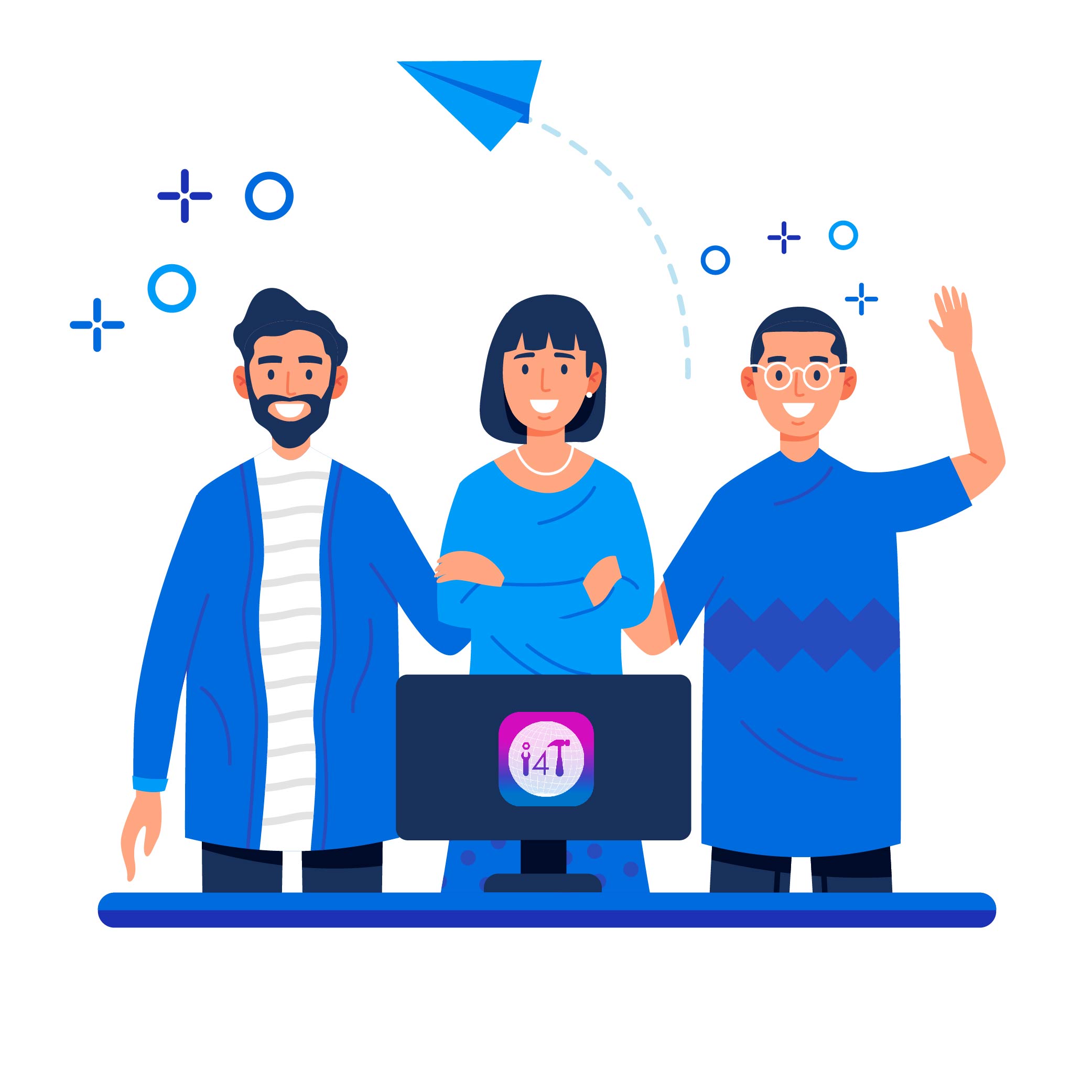
With our cutting-edge technology and in-depth knowledge of how the Field Service Management sector operates, the i4TGlobal Team loves to share industry insights to help streamline your business processes and generate new leads. We are driven by innovation and are passionate about delivering solutions that are transparent, compliant, efficient and safe for all stakeholders and across all touch points.