Are you running a field service business? Then, efficient inventory management can be a game changer for your business. This is because an efficient inventory management system will help you to reduce waiting time, and wastage and minimize costly emergency runs.
An efficient inventory management system will ultimately help your business complete the jobs on time and meet the customers' expectations.
Do you want to learn more about it? Then, keep on reading this article on inventory management, its importance, best practices, and many more.
What is inventory management?
Field service management (FSM) is evolving and becoming more competitive day by day. Therefore, efficient inventory management is critical to stay on top of your business. So, what is inventory management?
It is the continuous process of handling the goods and materials essential for your field service operations. This includes planning, buying, storing, and distributing these items so that they’re readily available when needed.
The importance of effective inventory management in the FSM industry
Field service management (FSM) is evolving and becoming more competitive day by day. Therefore, efficient inventory management is critical to stay on top of your business. So, what is inventory management?
It is the continuous process of handling the goods and materials essential for your field service operations. This includes planning, buying, storing, and distributing these items so that they’re readily available when needed.
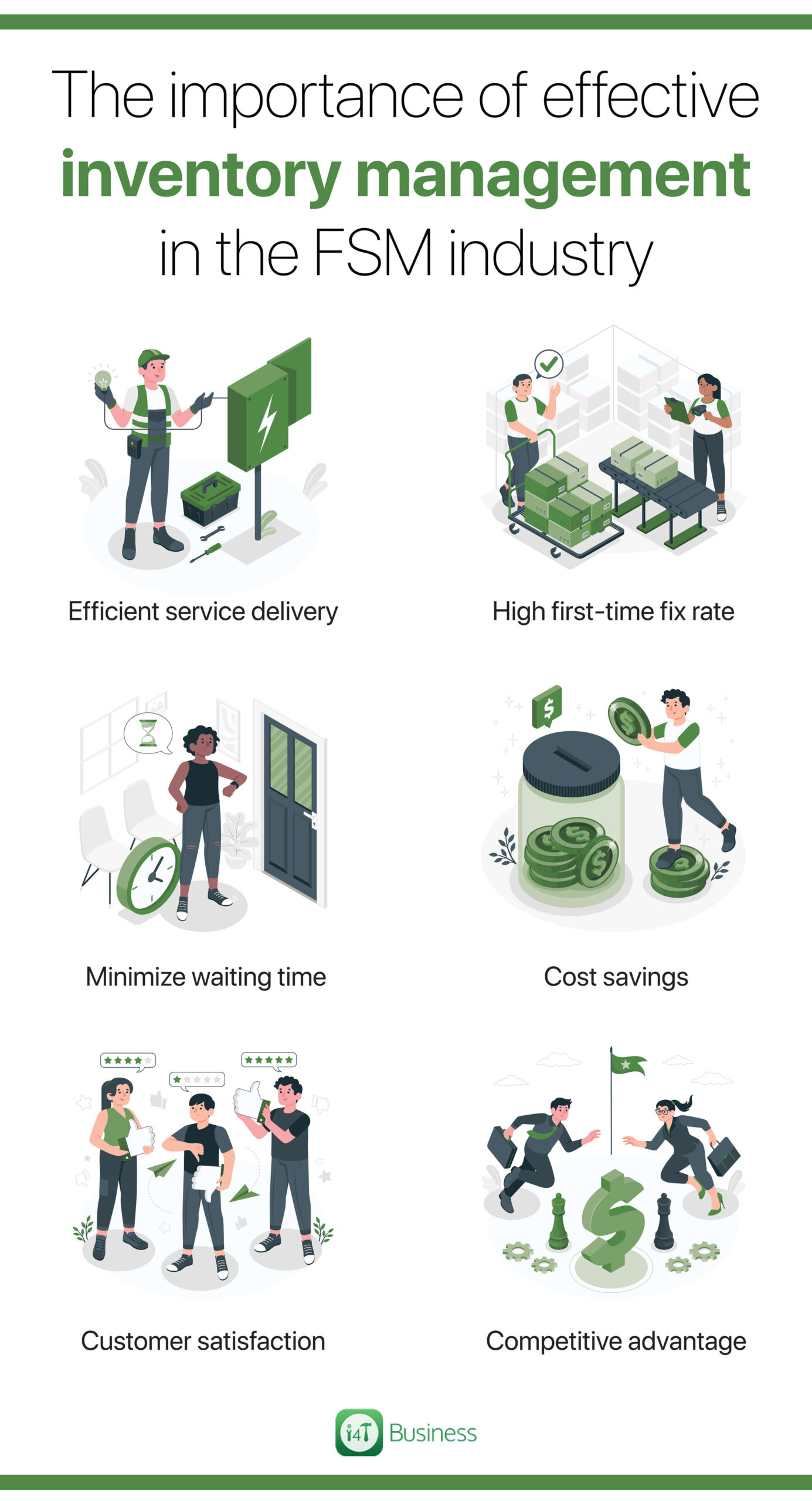
1. Efficient service delivery
This will ensure that field service technicians can access the right parts, materials, and equipment when needed. Therefore, technicians can deliver the service quickly and solve the customer’s issues without any delay.
2. High first-time fix rate
It should be a primary goal in your field service business to have a high first-time fix rate. This means resolving the customer’s issue on the first visit itself. Effective inventory management significantly improves your chances of achieving this goal by ensuring that technicians have the necessary components on hand.
3. Minimize waiting time
High waiting times can be costly for your business and your customers. Effective inventory management can help to minimize this waiting time. This is because this process will ensure the right material is available at the right place and at the right time.
4. Cost savings
Effective inventory management is about maintaining sufficient stock to meet service demands. It will help to avoid overstocking, which could increase your storage costs. In summary, this will ensure you have the necessary materials to meet customer demand while reducing unnecessary costs.
5. Customer satisfaction
As you know, a happy customer is a loyal customer. Inventory management helps to make customers happy by doing a smooth service delivery and fixing issues the first time.
6. Competitive advantage
Efficient inventory management can help you to be different from your competitors. This is because you can give a better service by having the right parts on hand and serving the customers well.
What are the challenges of inventory management?
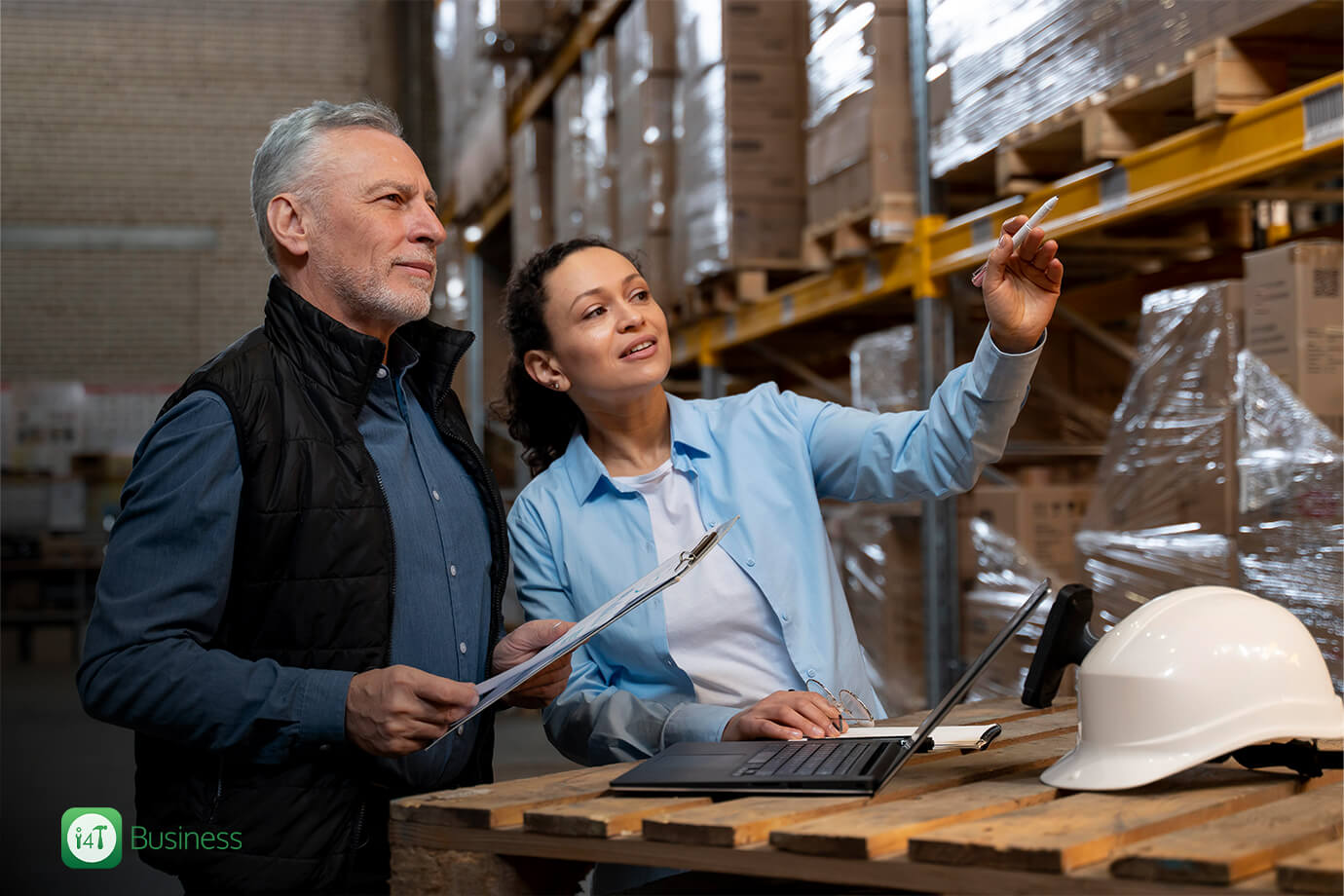
Efficient inventory management is crucial for the success of a field service business. However, it has its challenges. Let’s take a look at these challenges one by one and identify their impact on your business.
1. Difficult to forecast the demand
It might be difficult to determine the demand for certain materials correctly. This is mainly due to changes in customer needs, seasonal fluctuations, and unexpected equipment failures.
When you cannot forecast the demand correctly, it can lead to overstocking or understocking of inventory.
As you know, having more stock can hold up capital and increase storage costs. On the other hand, lower stocks can lead to delays in service, frustrate the customers, and you might miss service opportunities.
2. Material availability and lead times
Field service technicians might need immediate access to certain parts and equipment for repairs or maintenance. If it takes a long time to get these parts, technicians cannot provide services on time.
These delays will increase customer waiting time and negatively impact customer satisfaction. Sometimes, if the customers are not satisfied with a service, they may seek alternative service providers.
3. Limited storage space
Field service companies may face problems when finding storage space for their inventory. Limited storage can force companies to be selective about the inventory they maintain. This may affect the ability to meet various customer demands at the same time. In other words, this can affect the range of services your business can offer.
4. Stocking costs
As you know maintaining inventory can hold back your capital and raise your costs. But what are these costs? They are transport costs, storage costs, insurance, etc. Therefore, maintaining an excess inventory to meet every possible need can burden your finances.
This is because high stocking costs can reduce your profits. It will limit your ability to invest in improving other aspects of your field service operations.
What are the types of perpetual inventory management systems
Now, you might wonder what perpetual inventory management systems are. These systems can track and manage inventory in real-time. Further, they help technicians to get the right parts and materials when they need them. Let’s look at some different types of modern perpetual inventory management systems.
1. RFID-based systems (Radio-Frequency Identification)
RFID-based systems are highly effective for FSM, especially in industries where it is crucial to track assets and components in real-time. Field service technicians can use RFID tags to quickly locate and identify specific items in their inventory. This technology is highly valuable when dealing with a large and diverse range of equipment and parts.
2. Barcode scanning systems
This allows technicians to scan barcodes on inventory items, and update them instantly in the inventory management system. This system is user-friendly, cost-effective, and well-suited for maintaining accurate inventory records.
3. IoT-integrated systems (Internet of Things)
IoT-integrated systems are becoming highly popular in FSM. You can attach IoT sensors to equipment and parts to get real-time data on their condition. You can use this data for maintenance or replacement of the equipment. Further, it will help improve the performance of the equipment and reduce breakdowns.
4. Cloud-based inventory management software
Cloud-based inventory management software provides remote access to inventory data. This allows field service technicians and managers to view, update, and track inventory from anywhere. Cloud-based inventory management software will improve teamwork and ensure that everyone is working with up-to-date information.
5. AI-powered systems
AI-powered systems are particularly useful for maintaining the best inventory levels and predicting demand. These systems analyze historical data and usage patterns to make proactive recommendations. It helps field service companies maintain the right amount of inventory to meet customer needs while minimizing excess stock.
6. Mobile applications for inventory management
Mobile applications for inventory management empower field service technicians to manage their inventory on the go. They can access real-time information, update inventory levels, and place orders for replacements while in the field. This will reduce delays and ensure they have the right parts for the job.
Signs that your current inventory management system is outdated
When your inventory management system is outdated, it can affect efficiency and increase your cost.
It can also affect customer satisfaction badly. Therefore, you should look for signs that tell your system when your inventory management is outdated. Let’s look at some of these common signs.
1. Inaccurate or outdated inventory records
Is there a difference between what your system says you have in stock and what’s available? Then, it’s a clear sign that your system is not keeping up with real-time changes. Further, manual data entry may have errors. Therefore, if you have to update or enter data manually, it is time to upgrade.
2. Limited access
Does your system have remote access or mobile functions? If not, field service technicians may struggle to access and update inventory data while on the go. This is a clear sign that you should upgrade to modern technology.
3.Poor integration
An outdated system may not integrate well with other business applications. These applications may include accounting, customer relationship management (CRM), or field service management software. This can affect the smoothness of your operations.
4.Lack of automation
Automation is crucial for modern inventory management. Your system is not efficient if it doesn’t automate key tasks like reordering stocks when they are low. An outdated system may not allow you to track the usage patterns of inventory items. This is a clear sign that you should upgrade your system.
5.Long lead times for reports
You should have a quick and efficient system to generate reports on inventory data or usage history. If it takes more time to get such reports, your system needs an upgrade.
Conclusion
Inventory management is an important function in a field service management business. It will ensure that the right material or part is available at the right time and in the right place. As we discussed before, effective inventory management will help to minimize costs and improve service delivery. It will also help to improve customer satisfaction.
Inventory management comes with its challenges. There are modern technologies in inventory management that will help tackle these challenges. Keep in mind to watch out for the signs that indicate you need to upgrade your inventory management system.
If you are looking for a standard inventory management system, you should try out i4T Business Pro. It has an easy-to-use interface so that you can use it smoothly without any difficulty. Contact us today to get a free trial version and take your asset management system to the next level.
FAQs
It will automate tasks, provide real-time tracking, and offer insights into usage patterns. All of these will increase your efficiency.
It will reduce manual errors, optimize inventory levels, and enable data-driven decisions. This helps businesses to lower their costs.
Yes, it can. Inventory management ensures quick service delivery, high first-time fix rates, and minimizes waiting time. All of these can improve customer satisfaction.
IoT systems provide real-time data on equipment conditions and usage, allowing for proactive maintenance, reducing downtime, and improving customer service.
Data analytics help optimize inventory levels, make data-driven decisions, and improve overall efficiency.
Hot off the press!
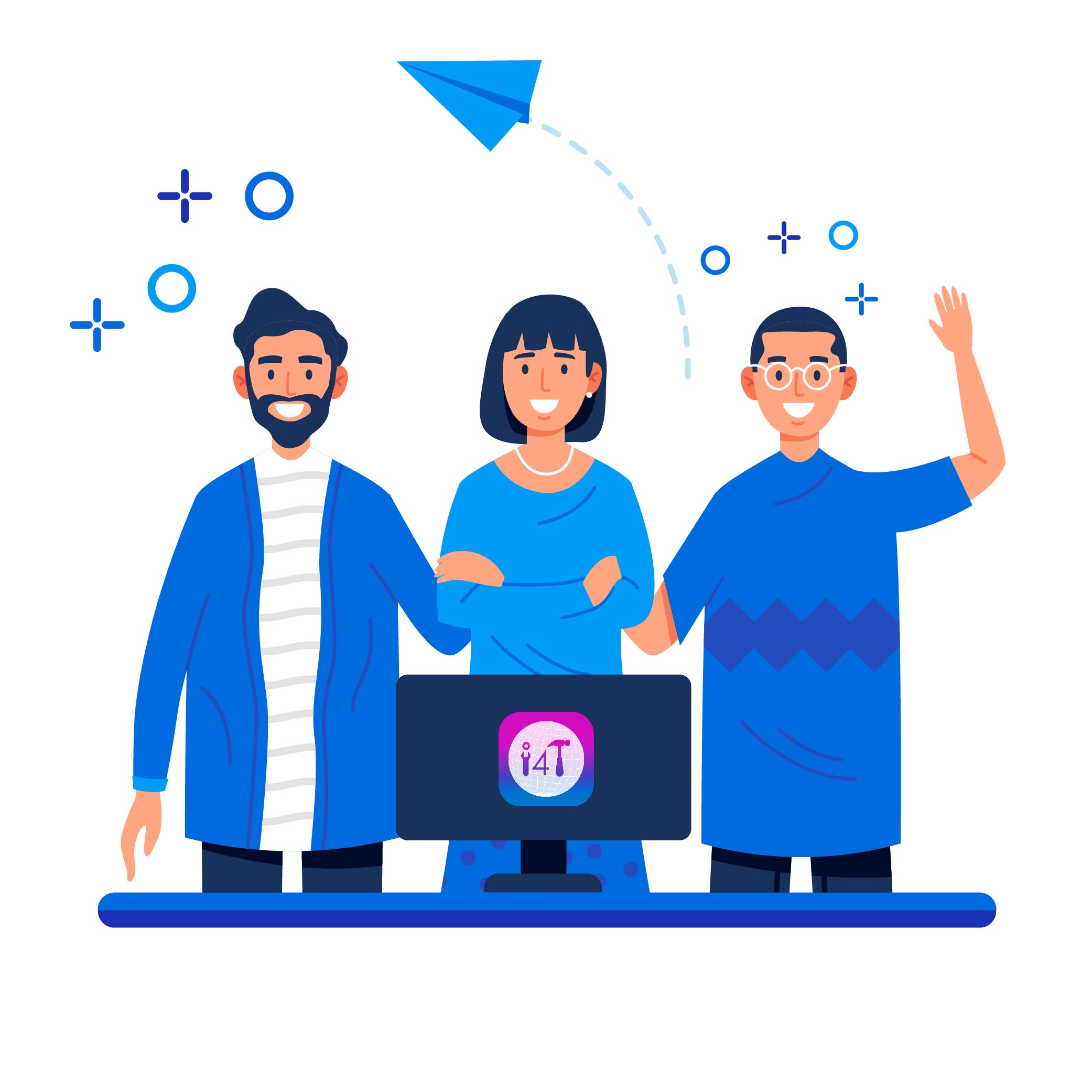
With our cutting-edge technology and in-depth knowledge of how the Field Service Management sector operates, the i4TGlobal Team loves to share industry insights to help streamline your business processes and generate new leads. We are driven by innovation and are passionate about delivering solutions that are transparent, compliant, efficient and safe for all stakeholders and across all touch points.