All businesses have only so much time, money and people to be allocated to carry out certain tasks. This means that businesses need to give more attention to tasks that can directly impact business continuity.
Risk-based maintenance (RbM) is one such approach to facility maintenance management that prioritises maintenance work based on the risk a certain incident carries and its consequences.
In this article, we will explain what risk based asset maintenance is and why it is so important. We will also take you through a step by step process of creating a risk based asset maintenance management plan. We will discuss the advantages and limitations of this approach and how using a CMMS software can help. Finally, we will determine if this is the right strategy for your business.
What is Risk-based Asset Maintenance and Why is it Important?
The end goal of risk-based maintenance is to minimise asset failure while keeping maintenance costs to the lowest.
Risk-based Maintenance Definition
risk-based maintenance works to find and implement the most economical use of your resources while increasing the asset’s reliability and useful life.
While these assets vary from industry to industry, some examples include:
- HVAC, lighting, electrical and plumbing systems
- Production line machines in manufacturing facilities
- Fleet maintenance in transportation industry
Risk-based asset maintenance is generally carried out in two phases:
- Carrying out risk assessment of all the assets
- Planning out maintenance tasks on priority basis
Importance of Risk-based Asset Maintenance
Risk-based maintenance is a kind of preventive maintenance technique. By giving priority to the most critical assets, it ensures that potential problems are detected and taken care of before they actually happen.
Risk-based maintenance considers the probability of failure and the consequences of failure:
Probability of Failure
The premise behind evaluating the probability of failure is considered by factoring the age of the asset, the frequency of use, the time of use and the environment where the asset is located. For example if an equipment is placed in a location which has high moisture content and dust, it might render it faulty earlier than its expected useful life.
Consequences of Failure
Consequences of failure considers the cost of repair if the asset in question breaks down. Facility managers should be asking questions like:
- How much is it costing the business in downtime?
- What is the cost of worker idle time?
- How much will it cost in repairing the equipment?
- What are any health and safety risks associated with the faulty equipment?
- Is the equipment breakdown acting as a bottleneck for other operations on the facility?
Step by Step Approach to Risk-based Maintenance

Risk based maintenance requires businesses to evaluate the risk of the assets, that could impact business continuity in case it fails.
To do this, a business has to carry out the following steps:
1. Collect Data on all the Equipment
You can use a computerised maintenance management system to collect data on your assets in use and how much they are costing you to run them.
The data you are aiming to collect here includes:
- The age of the equipment
- How often is it failing
- How much time it take to fix them
- What is the cost of failure in terms of idle staff, delay to market, interruption to other processes, repairs.
- How often is maintenance carried out on each of the equipment
2. Calculate the Risk of Failure and the Consequences of Failure
Calculating the risk of failure requires you to ask questions like:
- What is the likelihood of the machine to breakdown
- What factors could make the machine to fail
- How often it might fail
Now turn to the second part, which is the consequences of failure:
Ask, if the equipment fails, by how many days with the product be delayed, how many hours would be wasted or how much it cost in repairs?
3. Give a Rank to Each Risk and its Consequence
Score of risk probability:
- Equipment breaks down, once in 2 years.
- Equipment breaks down, once in 1 year
- Equipment breaks down, once in 6 months
- Equipment breaks down, once in 3 months
- Equipment breaks down, once every month.
Now assign the risk score to the trucks:
Truck A: Score 5
Truck B: Score 2
Truck C: Score 4
Score of risk consequences
- Less than $25,000 in annual repair costs
- Between $25000 to $50,000 in annual repair costs
- Between $50,000 – $75,000 in annual repair costs
- Between $75,000 to 100,000 in annual repair costs
- More than $100,000 in annual repair costs
Now assign the consequence score to the truck:
Truck A: Score 4
Truck B: Score 1
Truck C: Score: 2
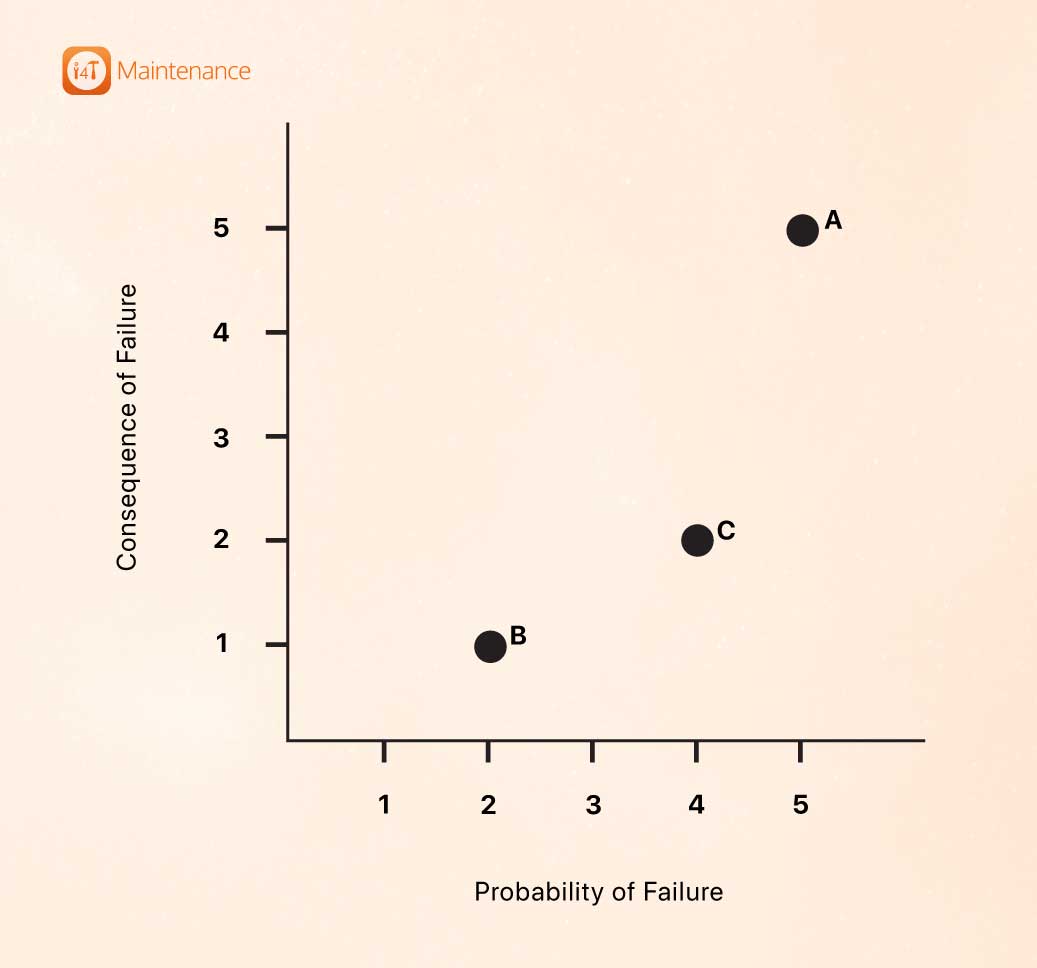
4. Develop a Risk-based Maintenance Plan
Now that you know which of your equipment lies in the high risk zone, you need to create a risk-based management strategy to curtail the risk of your assets you have just evaluated.
Here, it’s time to think about which maintenance strategy best suits your needs. High risk assets should follow a condition-based maintenance plan and schedule accordingly. Create a risk mitigation plan. Start small with a small number of critical assets, review and reassess effectiveness of your strategy and manage it on an on-going basis.
Risk-based Maintenance Advantage and Disadvantage
Advantages of Risk-based Maintenance:
- Improves safety and reliability of your assets
- Prolongs the life of your assets
- Puts your limited resources to their best use
- Eliminates high cost – low value maintenance work orders
- Brings down risk of equipment failure to the acceptable level
- Is relatively straight forward
Disadvantage of Risk-based Maintenance
- Requires significant initial planning by dedicated personnel
- Needs to be updated periodically based on variables such as asset age or usage.
- Can be complex to manage across departments
Using a CMMS for Risk-based Maintenance
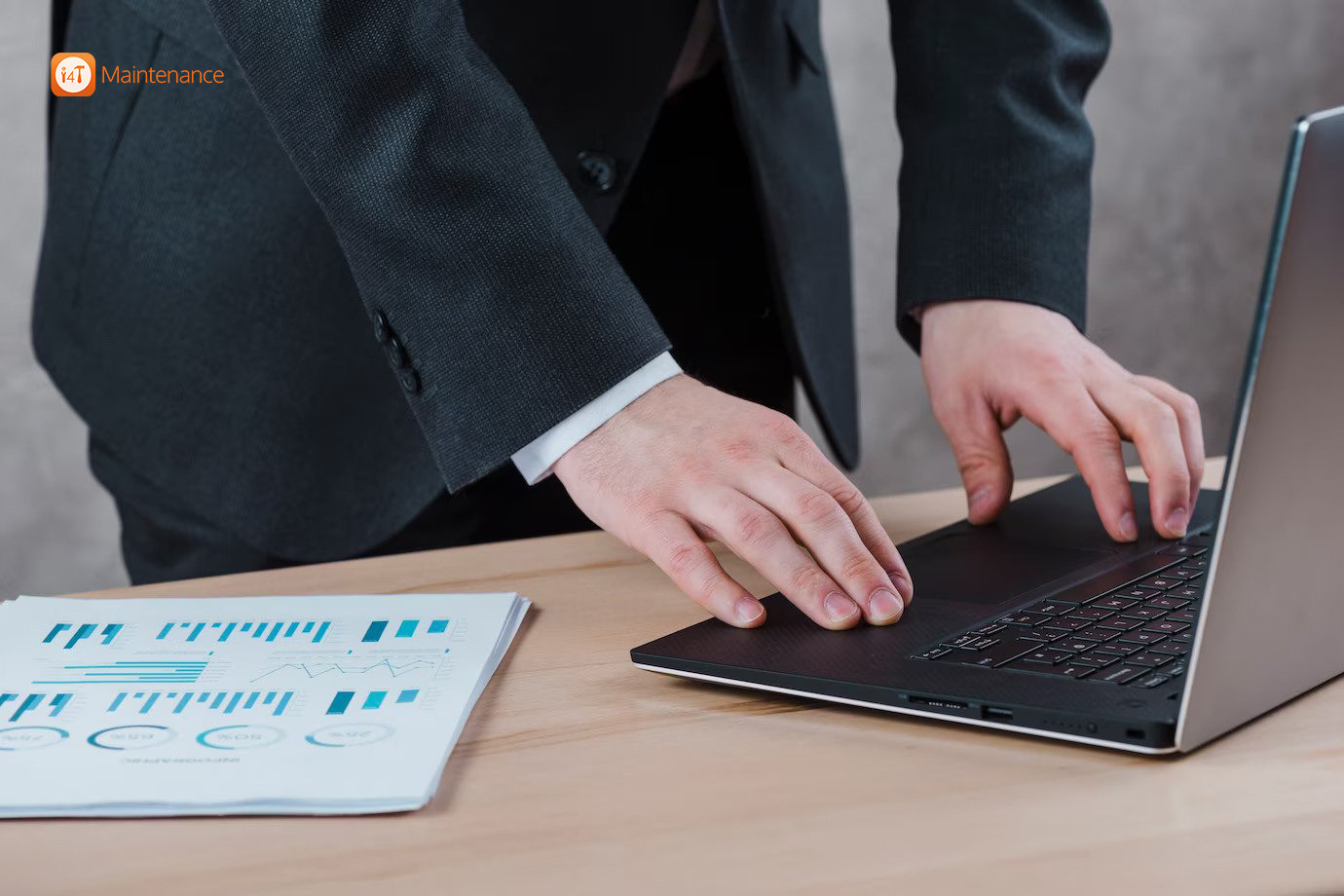
a good CMMS solution should be able to utilise data such as failure histories, interdependent assets and risk scores to schedule maintenance work orders.
A CMMS solution can help maintenance managers:
- Streamline the entire risk based management process through a single platform with workflow standardisation and automation.
- Analyse historical data from past inspections and completed work orders providing deep insights into effective risk evaluation.
- Helps identify potential problems in advance and their possible solutions for you to implement a preventive maintenance strategy.
- Helps you comply with regulatory requirements without having to spend additional time and money on self-assessment.
- Generate detailed reports to maintain record of asset failures and actions taken for future reference.
i4T Maintenance is one such CMMS solution for facility maintenance managers, helping them with the implementation of risk based-maintenance strategies for their business.
Is RbM the right strategy for your business?
- Business with high use, highly critical machinery: An example of this could be an oil processing plant that uses a machine to purify the oil. Your 100% operations and business depends on this machine and you just cannot afford it to go down at all.
- Business with very costly machinery: Not doing risk based maintenance of expensive machinery can result in very high repair or replacement costs.
- Business that does not have any other maintenance strategy in place: This can be your go-to plan if you have just started and want to keep your critical assets delivering 100% uptime.
- Business with limited resources: If your maintenance budget is not high and you cannot afford to put a predictive or preventive maintenance strategy in place, risk based management can be the way to go.
Final thoughts
Risk-based maintenance is a maintenance strategy that prioritises maintenance of assets based on the risk score they carry. Its most prominent benefit is that it handles maintenance work in the most economical way, putting the resources only where needed.
If risk-based maintenance is your chosen maintenance strategy, you should consider using a CMMS system such as i4T Maintenance to gather quality data, prioritise resources, streamline your maintenance work orders and manage your critical assets better.
Hot off the press!
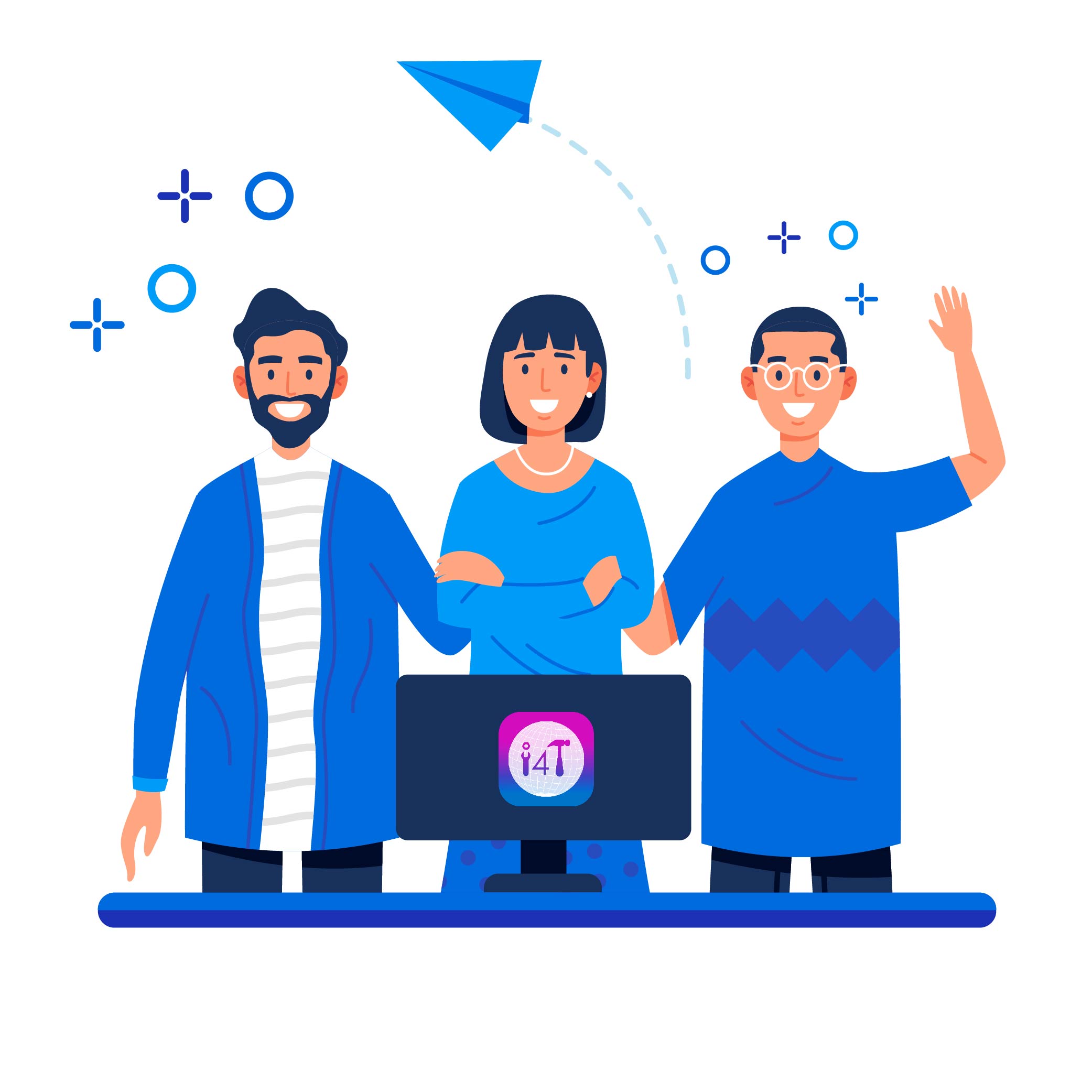
With our cutting-edge technology and in-depth knowledge of how the Field Service Management sector operates, the i4TGlobal Team loves to share industry insights to help streamline your business processes and generate new leads. We are driven by innovation and are passionate about delivering solutions that are transparent, compliant, efficient and safe for all stakeholders and across all touch points.