Facilities managers will agree that maintaining equipment and systems is an essential part of ensuring their safety and functionality throughout the year.
Due to a lack of consistent, proactive repairs, deferred maintenance can waste thousands of dollars each year.
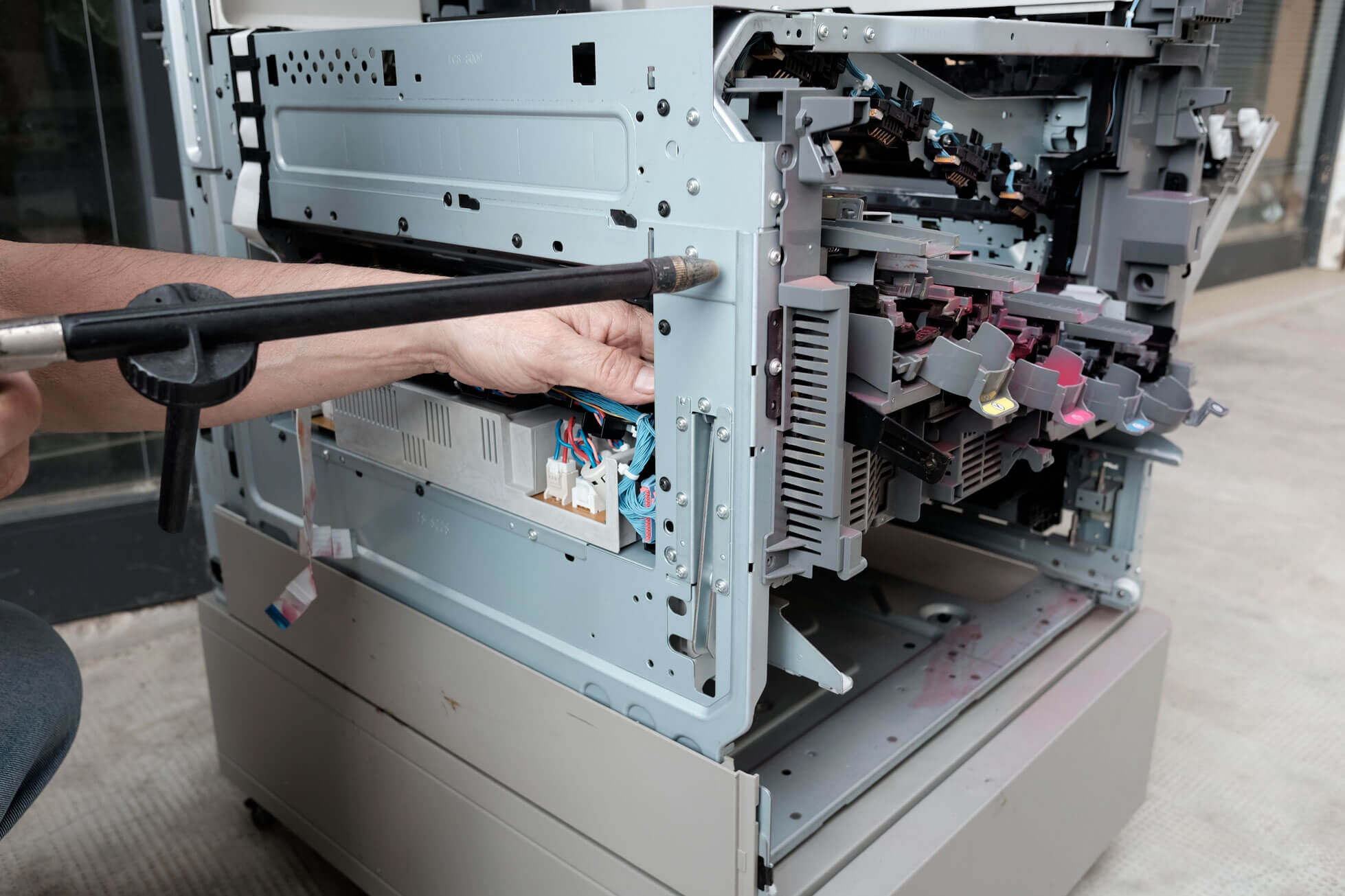
What is Deferred Maintenance?
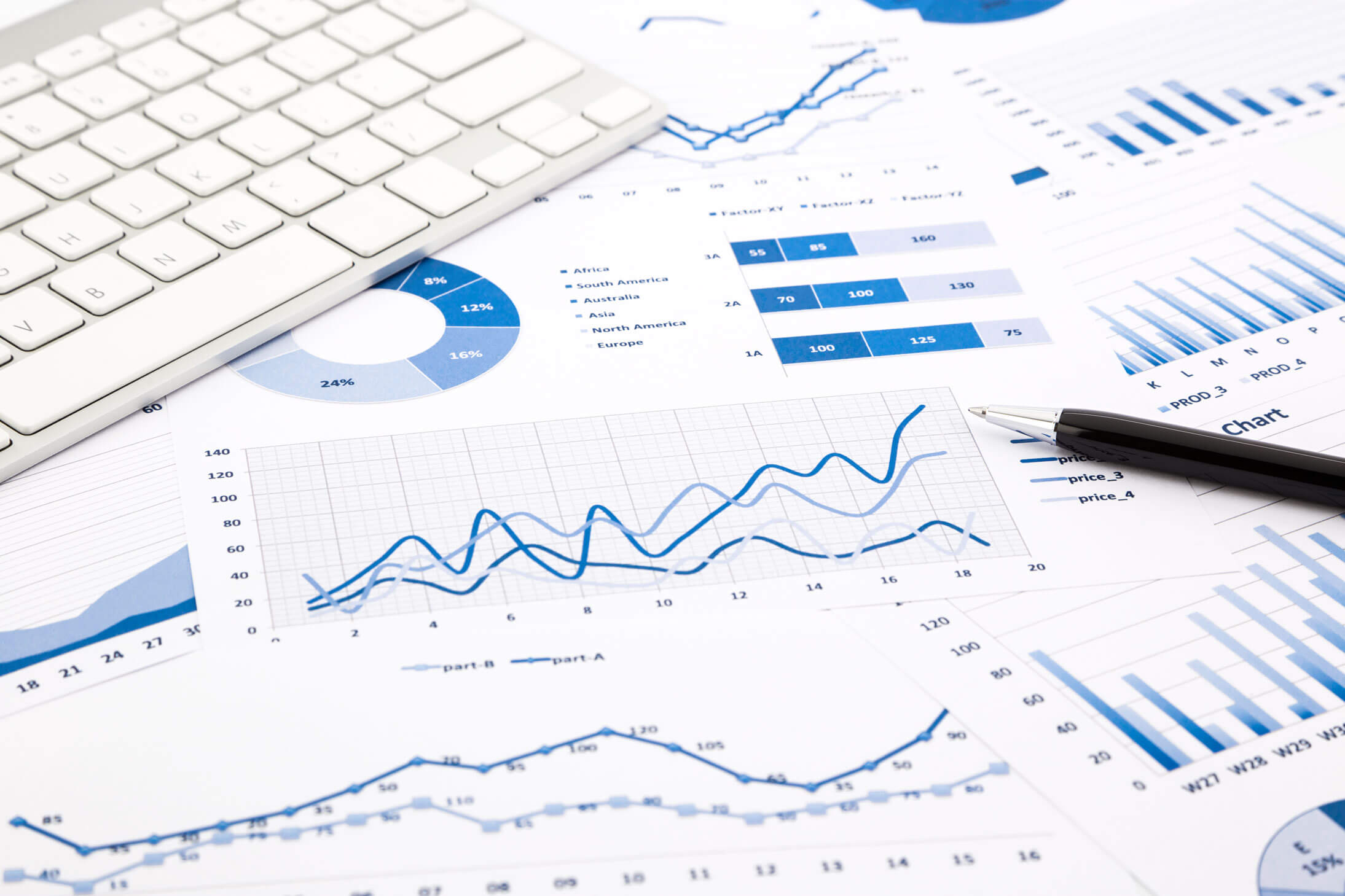
Common Reason for Backlog Maintenance
- Your maintenance team is working with a fixed or declining budget.
- Your organization lacks a reliable and consistent preventive maintenance strategy.
- Overworked and/or understaffed maintenance team.
- Your team lacks the knowledge or documentation required for conducting repairs.
- Your maintenance team lacks a good system for managing spare parts inventory.
Related Article: The Must-Have Skills and Qualities That Makes A Great Facilities Manager
What are the Risks of Deferred Maintenance?
A maintenance team's nightmare can be backlogged maintenance.
Not only will your organization be subjected to costly equipment failure, but it may also have to spend significantly more money on reactive maintenance. A minor repair can cause substantial damage if left unattended.
As a result, total repair costs rise dramatically. Deferred maintenance may also have unintended consequences, such as increased health/safety risks and decreased occupant satisfaction when equipment fails to function as expected.
Related Article: Allowing your Asset Run to Failure: Pros and Cons of RTF as a Maintenance Strategy
Costs and Consequences of Deferred Maintenance
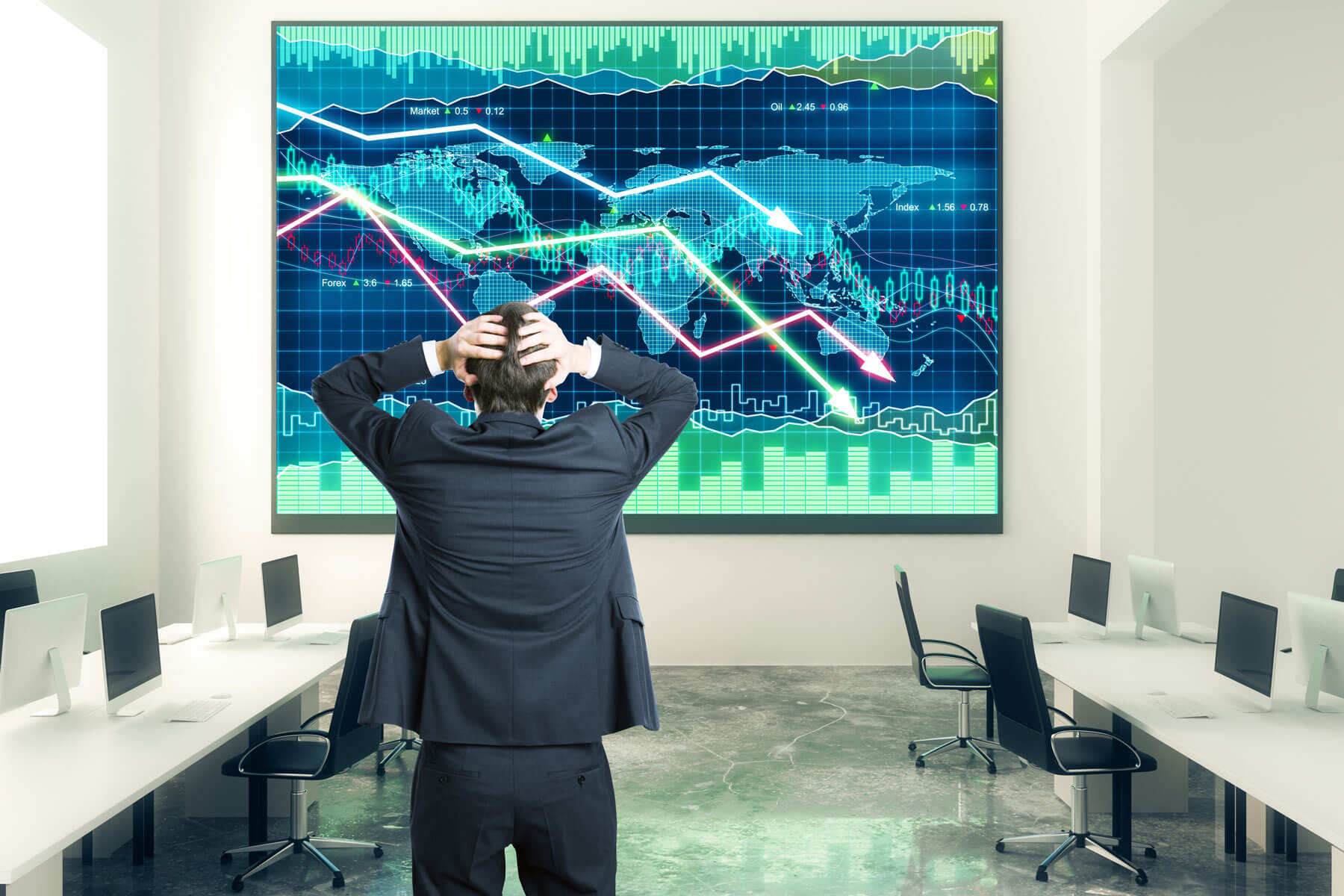
Here are ten ways that deferred maintenance can impact your company’s productivity and profitability:
1.) Safety Hazards
Employees and occupants can be physically harmed or injured if equipment fails.
2.) Health Hazard
Poor air quality, mold, mildew, and other health risks can result from occasional cleaning and inspections.
3.) Expensive Emergency Repairs
Unexpected repair costs can easily exceed preventive maintenance costs by hundreds, if not thousands, of dollars.
4.) Reduced Efficiency of Equipment
Machinery with dirty filters, worn-out belts, or loose parts will not perform optimally.
5.) Compliance Risks
Failure to pass safety and compliance inspections can result in fines of thousands of dollars.
6.) Asset life cycles will become shorter.
Assets that are subjected to heavy wear and tear are unlikely to last their full life cycles.
7.) Productivity Loss
Unexpected equipment downtime can have a negative impact on profitability and the bottom line of your company.
8.) Failure of the Entire System
Emergency asset replacement is stressful and can reduce maintenance reserves unexpectedly.
9.) Buildings of Poor Quality
Deferred maintenance can have a negative impact on building quality, as well as its ROI and overall value.
10.) Employee Burnout and Stress
Employee morale can be affected by the pressure to catch up on maintenance while dealing with limited resources.
Related Article: What is Preventive Maintenance? A Complete Guide to Preventive Maintenance
As this list demonstrates, putting off maintenance can lead to costly, time-consuming problems that are difficult to resolve. The good news is that with the right tools and resources, it is possible to move away from reactive maintenance and toward a more proactive approach to workflows.
How to Deal with Deferred Maintenance in Your Facility
Facilities Managers and teams have a number of options for breaking the cycle of deferred projects and backlog buildup that can assist them in overcoming their most pressing issues.
- Examine current maintenance processes and projects.
- Use software to centralize work orders.
- Maintain a record of all maintenance activities in a building infrastructure software platform.
- Sort your backlog of maintenance tasks into priority orders.
- Perform life-cycle cost analysis on critical equipment.
- Make your team’s preventive maintenance strategy effective.
- Be aware of the industry’s latest preventive maintenance techniques.
- Collaborate with your financial team to secure additional funding if necessary.
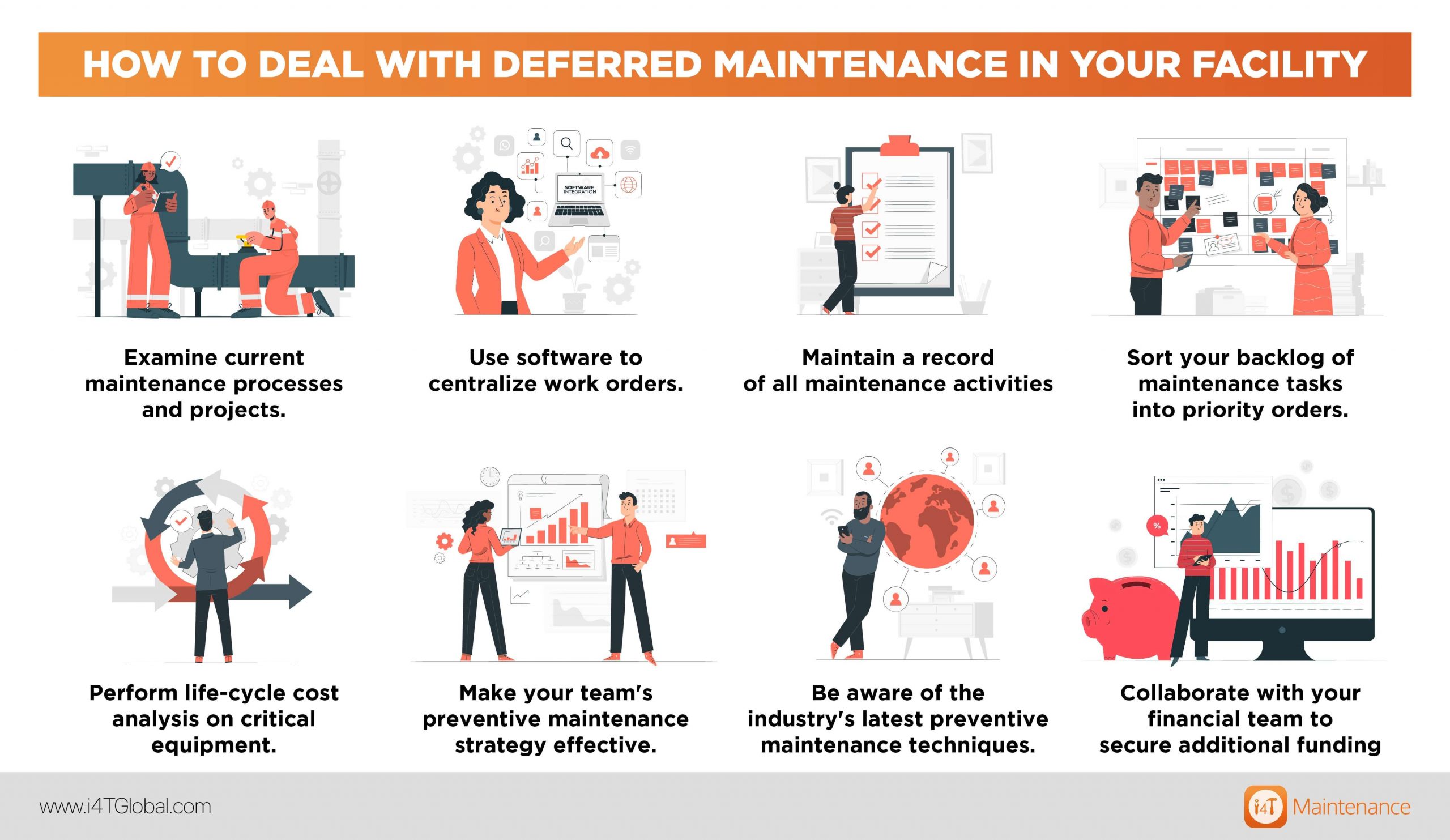
Implement your Maintenance Program with i4T Maintenance
Tight budgets and timelines usually drive reactive maintenance management rather than preventive maintenance management, but you don’t have to face these challenges alone.
i4T Maintenance Software provides various solutions that assist facility professionals in making data-driven decisions to address backlog maintenance lists and prevent future breakdowns.
Our SaSS Solution helps you to create preventive maintenance schedules that generate work orders automatically, allowing you to stay on top of proactive maintenance tasks and avoid them falling into your deferred maintenance list.
i4T Maintenance Comprehensive Dashboard gives you the insights you need to create accurate capital budgets now and in the future. Make decisions based on actual facility and asset condition and risk data, rather than industry averages.
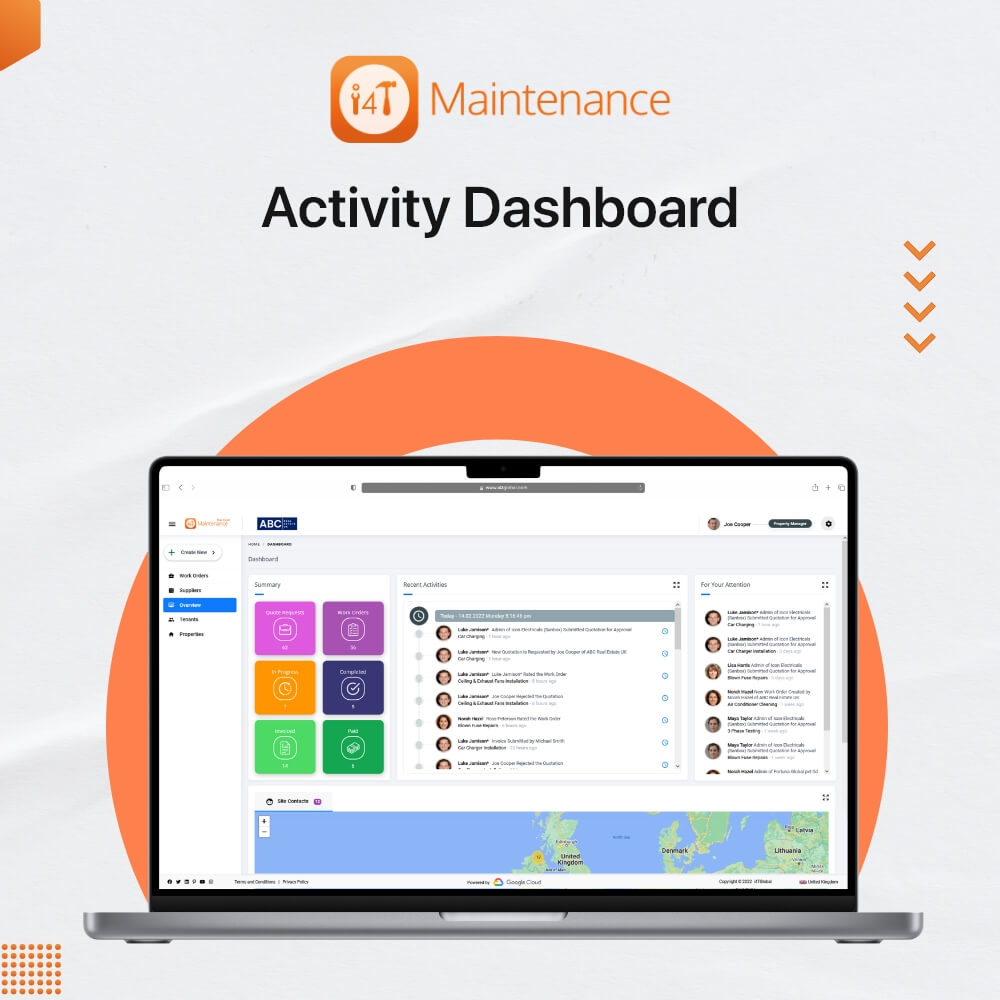
Prominent Features of i4T Maintenance
- Automated Work Order Management
- Real-Time Communication
- Customised Dashboard
- Effective Data Storage
- Detailed Reports and Analytics
- CMMS Mobile App
- Regional Compliance Management
Hot off the press!
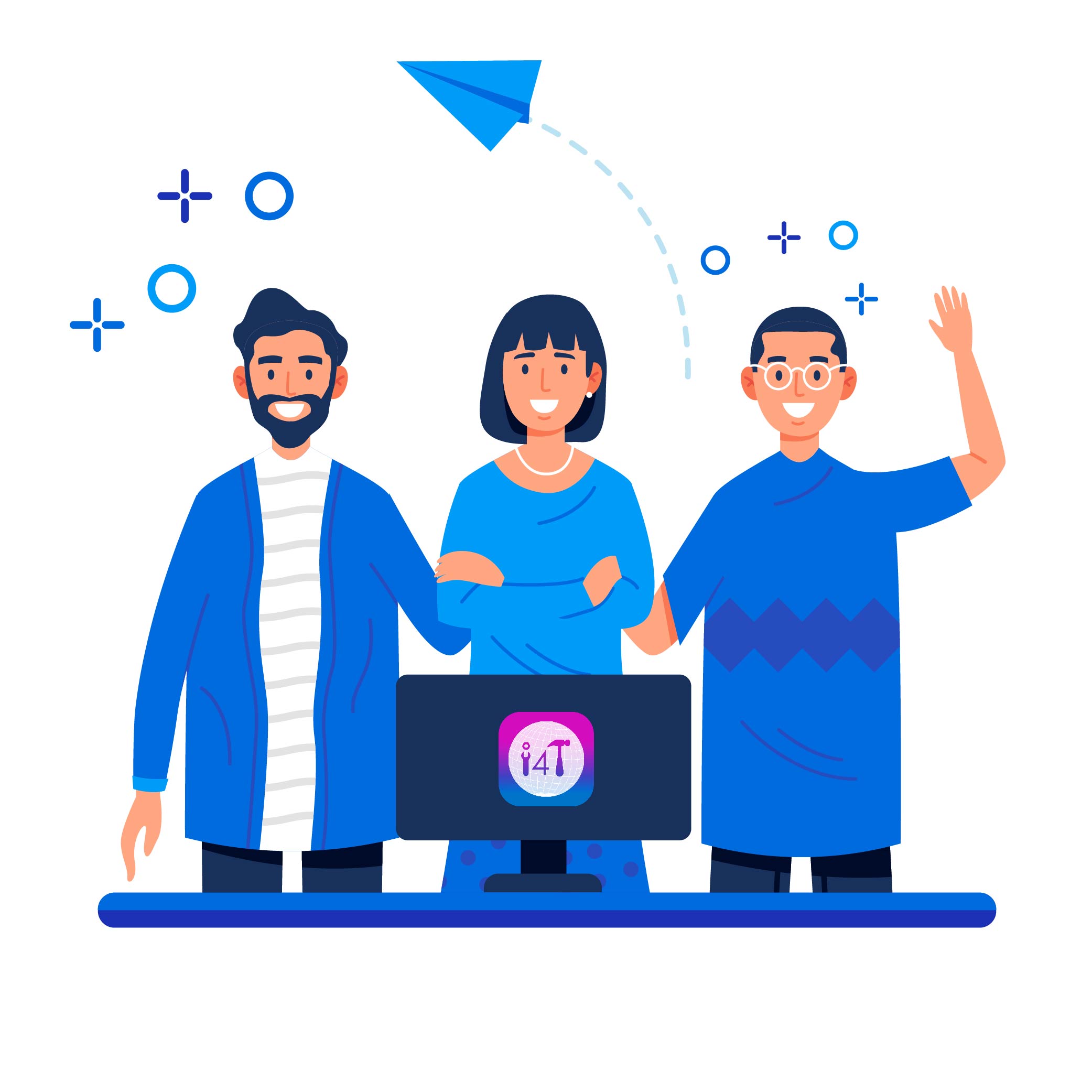
With our cutting-edge technology and in-depth knowledge of how the Field Service Management sector operates, the i4TGlobal Team loves to share industry insights to help streamline your business processes and generate new leads. We are driven by innovation and are passionate about delivering solutions that are transparent, compliant, efficient and safe for all stakeholders and across all touch points.