Run-to-Failure (RTF) Maintenance, also known as fit and forget maintenance, is a type of maintenance strategy that follows a simple formula: WAIT UNTIL IT FAILS.
It is critical to have sufficient spare parts and manpower in the arm to replace the failed part and maintain equipment availability when using the Run-to-Failure Strategy.
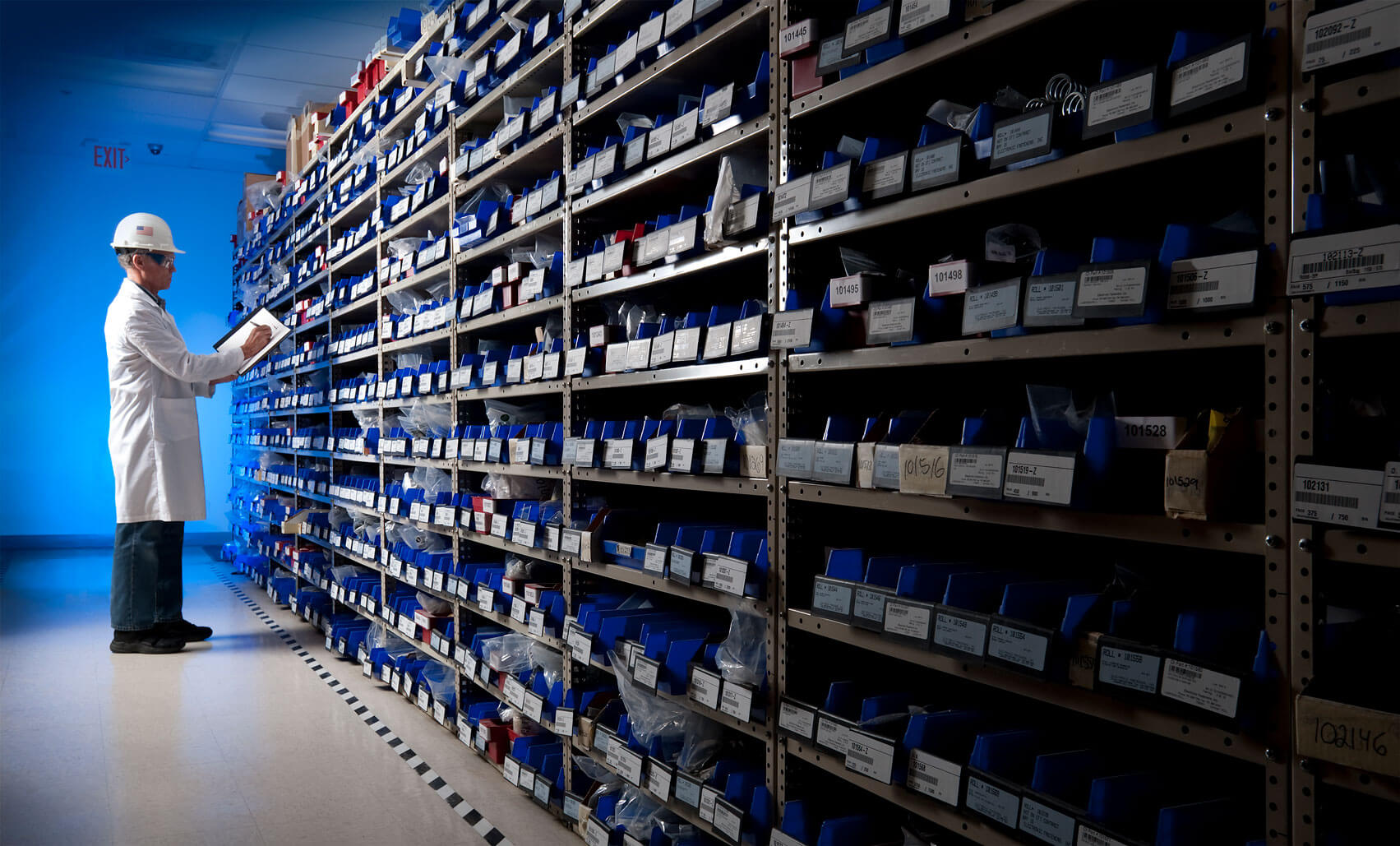
Although the Run to Failure Maintenance Strategy appears to be unplanned, it is actually a planned strategy designed to reduce equipment maintenance costs
Example:
The maintenance plan for a general-purpose light bulb.
The bulb is left on until it burns out. At this time, the asset repair plan is being implemented. A new light bulb is obtained from inventories and installed at a suitable time.
Here is a classified Run to Failure Maintenance Workflow:
- Stage 1: A new part is installed with visual support.
- Stage 2: Part performs as expected during its service life.
- Stage 3: Part's output falls below the acceptable levels.
- Stage 4: Part replacement work order is created.
- Stage 5: Implementation
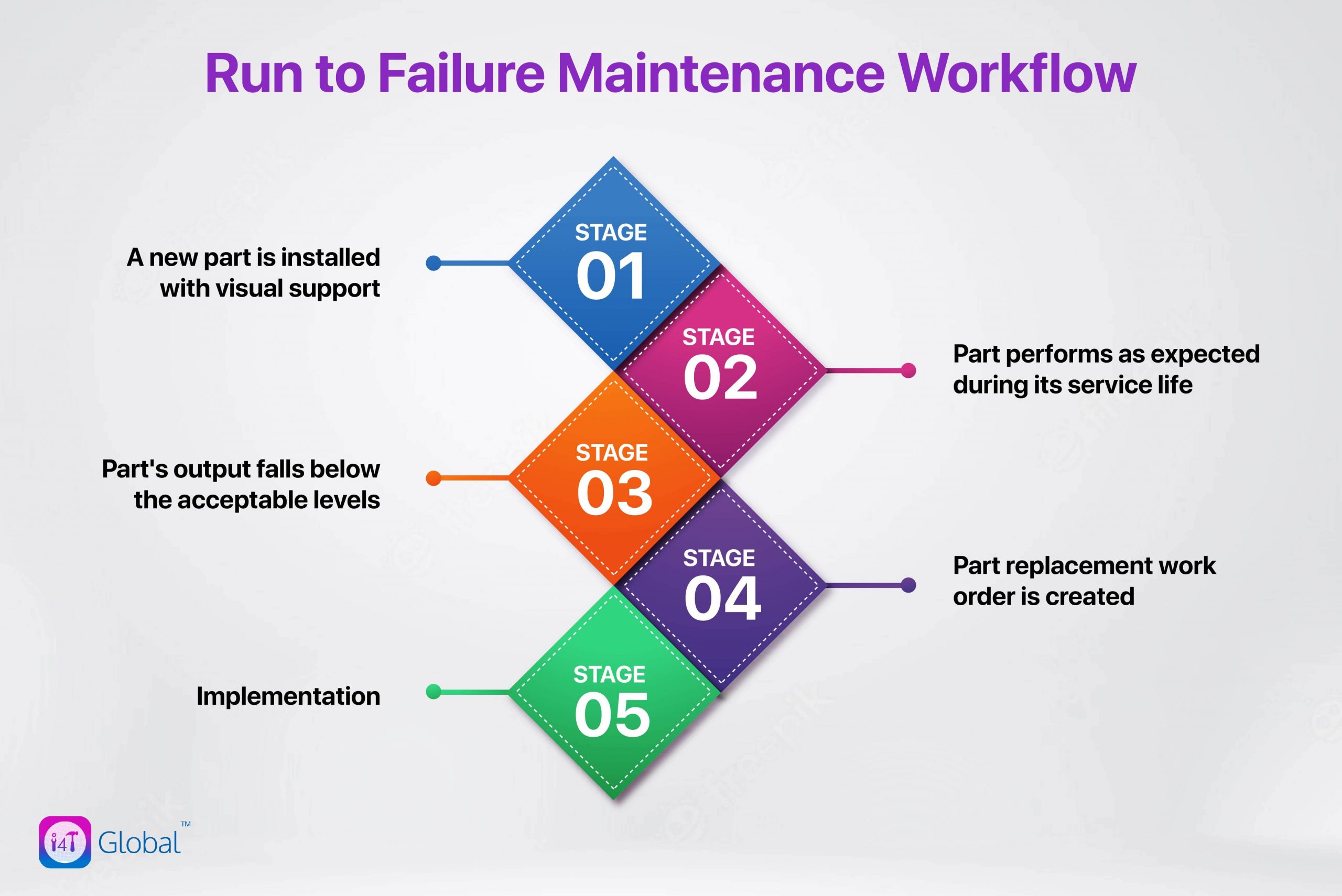
Now that we have a clear understanding of how the Run to Failure Maintenance Strategy works, let’s take a look at the pros and cons of this type.
Related Article: What is Preventive Maintenance? A Complete Guide to Preventive Maintenance
Pros of RTF as a Maintenance Strategy
1. Minimal Planning
2. Cost-Effectiveness
3. The Process is Straightforward and Simple to Understand.
4. Less Manpower is Needed
Cons of RTF as a Maintenance Strategy
1. Inconsistency
2. Unpredictability
Several failures are unforeseeable, that is, they cannot be predicted. As a result, it is impossible to predict when specific assets will need to be repaired or replaced.
As a result, it can be difficult to resolve issues or problems at times, and this can lead to further damage in the future.
3. High Inventory Costs
To account for intermittent failures, the maintenance team must keep spare parts on hand. Failures can sometimes cause more damage and necessitate more resources to repair.
This will result in an increase in repair costs. This increases production costs as well as labor costs associated with maintenance.
How Can the RTF Maintenance Strategy be Implemented?
When evaluating the applicability of an RTF maintenance strategy, four factors should be considered:
- Personnel Safety
- Production Downtime
- Equipment Reliability
- Asset Redundancy
A Run-to-Failure maintenance strategy is not an abdication of responsibility when it is used as part of a well-planned maintenance program, supported by defensible economic and safety analysis, supported by a powerful Computerized Maintenance Management System (CMMS).
Using CMMS to Plan your Run to Failure Maintenance Strategy
Maintenance AI Tools are increasingly being used in the operational management of machinery and equipment across all industries.
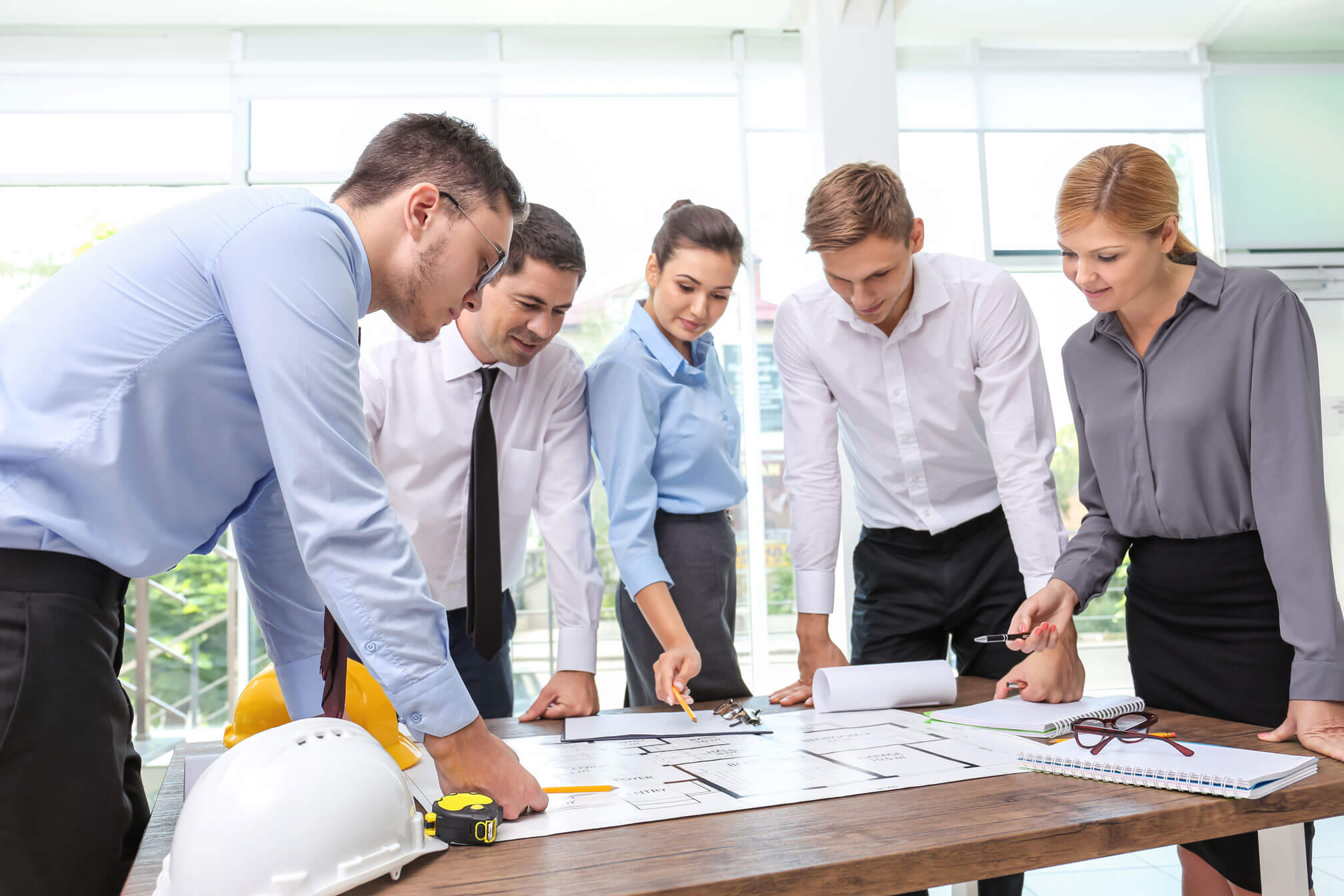
Investing in a good Computerized Maintenance Management System can quickly return you to control of your maintenance program and help you reduce costs.
Here’s a 10 Steps process for an effective RTF Strategy.
- Step 1: Identifying workflow failures
- Step 2: Deciding the best CMMS that fits your requirements.
- Step 3: Planning the transition period
- Step 4: Developing a maintenance plan
- Step 5: Creating an asset database
- Step 6: Recording maintenance, repair, and breakdown data
- Step 7: Establishing a job planning process
- Step 8: Use asset data to identify the gaps
- Step 9: Take necessary improvement steps
- Step 10: Set KPIs to monitor and measure the progress
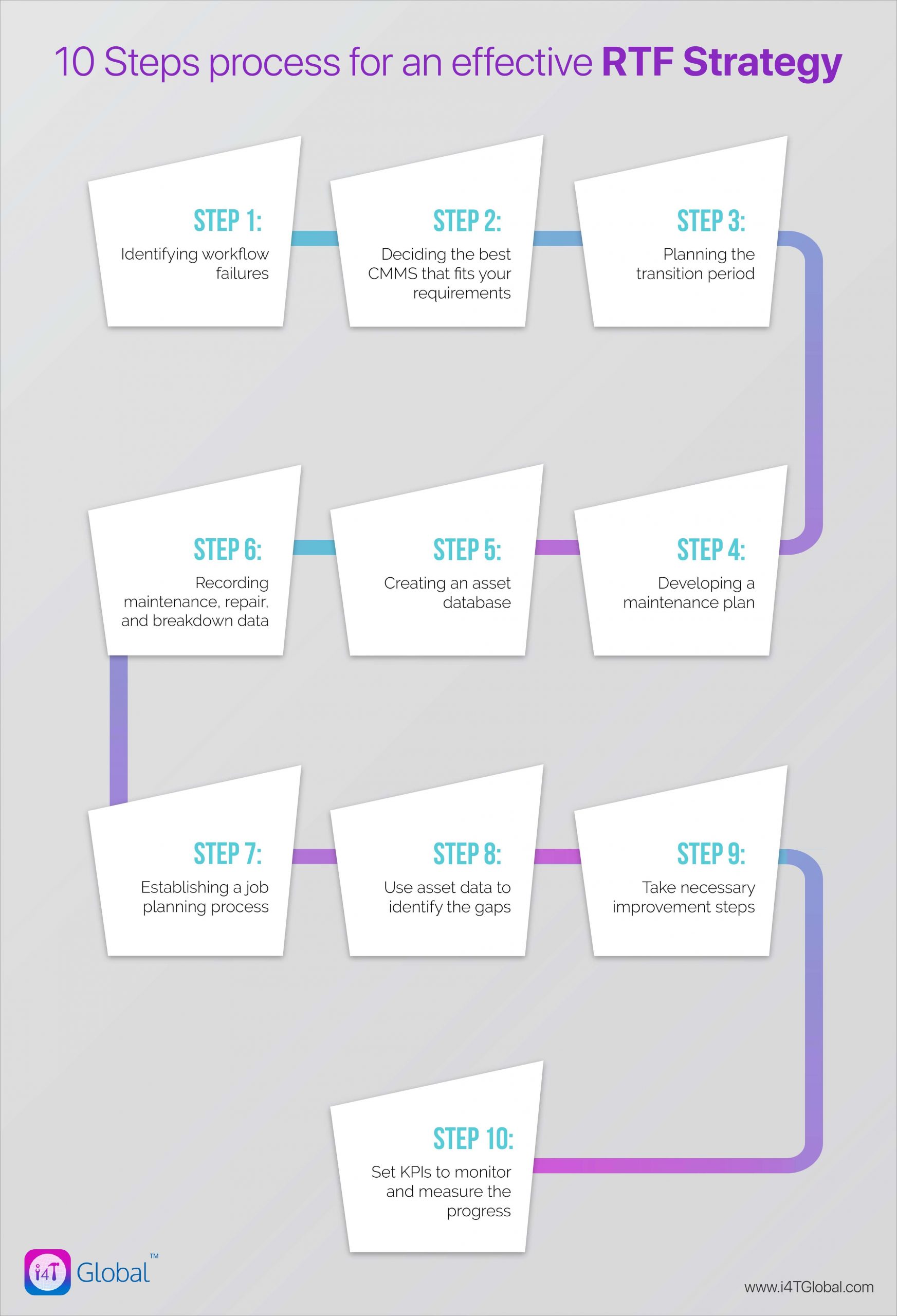
Related Article: A Comprehensive Guide to Choosing a CMMS Software
Planning your Run to Failure Maintenance Strategy with i4T Global
We place a strong emphasis on preventative maintenance for facilities management, field service, and property maintenance here at i4T Global. Our core mission includes ensuring that proper preventative care leads to cost savings and reduced downtime for our clients.
RTF maintenance is thought to be the most cost-effective type of reactive maintenance strategy. In essence, by using this system, you allow appliances and equipment to run without maintenance until they reach the end of their useful life. While this may seem unusual to our strategy, there are times when the RTF strategy is your best maintenance option.
A true RTF strategy is designed to reduce costs while also predicting service life to ensure you are prepared for failure. You can save money on preventative services by considering the service life and use of specific appliances and parts.
Using preventative maintenance, RTF, and other strategies in between will allow you to tailor your maintenance plan to your facility's specific needs.
There is no prepackaged maintenance schedule that will work for the same equipment and building. That is why it is critical to consult our i4T Global Team to determine what is best for your company.
i4T Global specializes in preventative maintenance, but we also handle routine RTF maintenance. We make your facility run more smoothly so you can focus on what is important to you.
Contact us right away to learn more about our preventative maintenance software!
You might also be interested inHow To Run Your Office’s Facilities Maintenance Efficiently? A Comprehensive Guide For Facility Managers
Hot off the press!
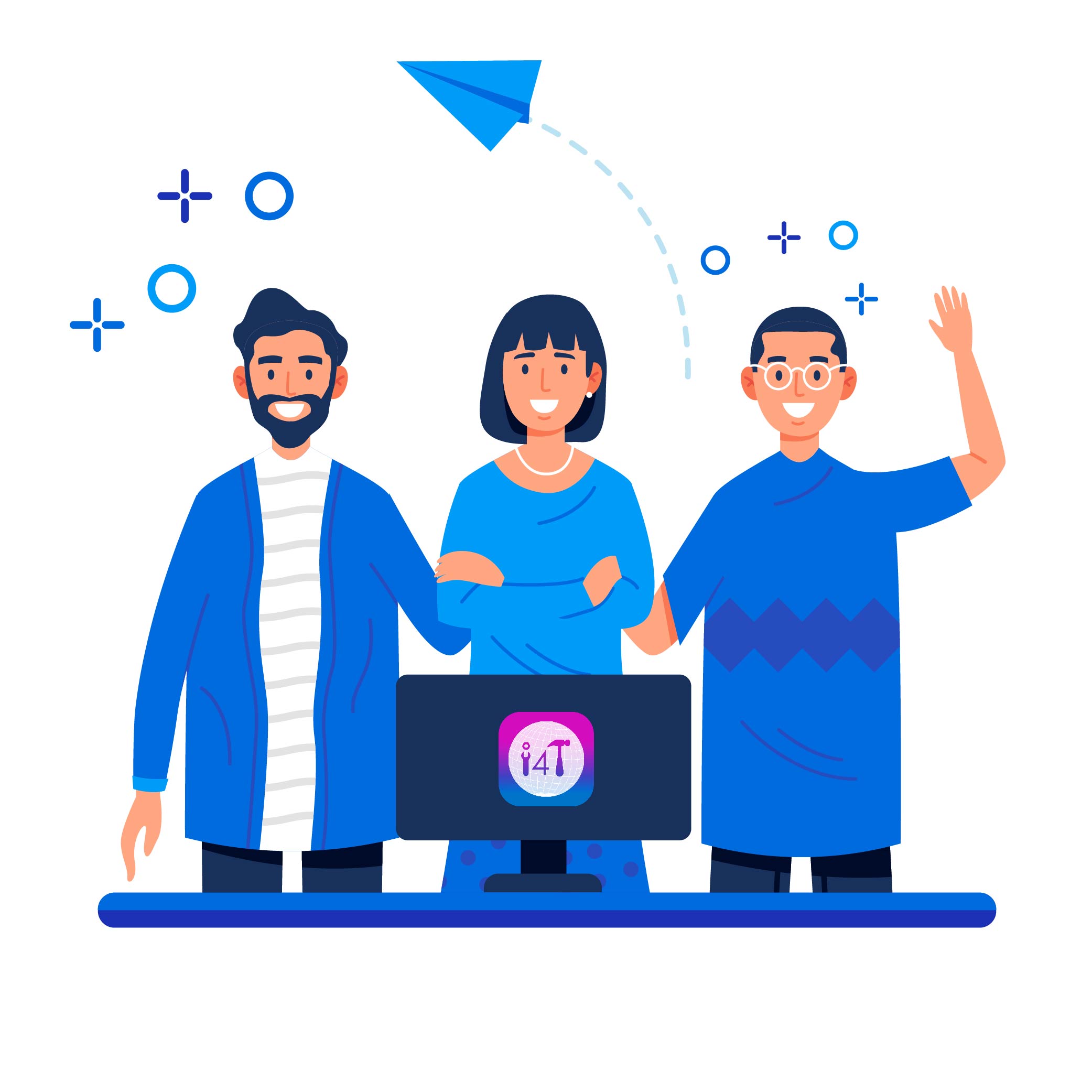
With our cutting-edge technology and in-depth knowledge of how the Field Service Management sector operates, the i4TGlobal Team loves to share industry insights to help streamline your business processes and generate new leads. We are driven by innovation and are passionate about delivering solutions that are transparent, compliant, efficient and safe for all stakeholders and across all touch points.