What are SOPs for Facilities Maintenance Companies
Maintenance SOPs are detailed documents that layout all the steps and instructions maintenance workers need to abide by while performing a certain maintenance task. Most companies have an SOP manual that explicitly outlines rules to be followed, conditions to be met and the quality standards that need to be maintained.
While some SOPs can be business specific, more often than not, these are industry standards set in accordance with the regulatory requirements.
Purpose of setting Standard Operating Procedures for Facility Maintenance Companies
SOPs in Facility maintenance services are a set of guidelines defining who does what, how and when. How can standard operating procedures help ensure legal compliance? They ensure that not only everyone understands them clearly, but also follows but also facilitates routine audits to ensure they are being followed correctly.
Additionally, the importance of safe operating procedures in the workplace cannot be stressed enough. Today, an increasing number of facility managers rely on Standard Operating Procedures to:
- Improve service performance by tracking and measuring efficiency
- Strengthen an organisation’s regulatory compliance
- Enhance overall productivity of all assets
- Maintain accountability and ownership of tasks
- Prioritise safety for occupants
- Ensure quality across the entire service delivery value chain.
- Streamline onboarding and training of new employees.
- Use as a reference when recreating processes in a new setting
- Audit processes against a certain standard and use of checklists
- Reduce miscommunication between all stakeholders.
- Streamline workflows across the organisation
- Eliminate errors or unnecessary steps in a process.
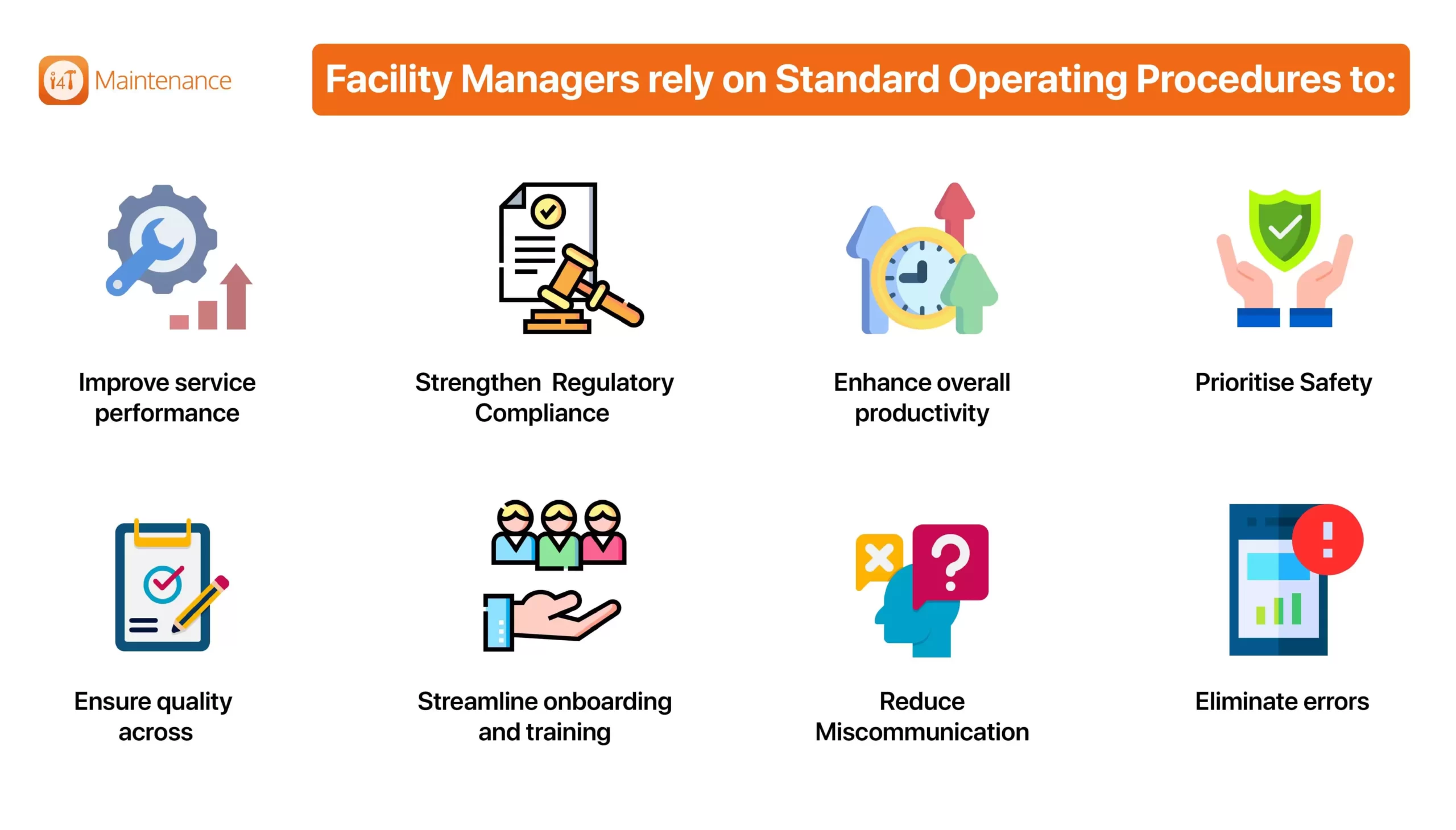
When set right, SOPs for facilities maintenance services streamline workflows and ensure there is no miscommunication between maintenance teams.
As a rule of thumb, SOPs are ideal for:
- Vertical organisations where processes flow from top to bottom.
- Organisations that need to carry out repetitive tasks day in and day out
The facility maintenance sector qualifies on both of these criteria. Hence, SOPs serve as a vital tool for maintenance managers to keep quality in check as workflows grow.
Steps to create an effective Maintenance SOP document
Provide clear directions
Stay to the point
SOPs must be created for a specific task. Try not to deviate from that task when steps are being explained in detail.
This helps you avoid scope creep. Precisely outline the process and assign roles and responsibilities. Too long or detailed instructions can leave the readers confused and cause misunderstandings when carrying out the task.
Facilities maintenance services SOPs should be simple
Talk to the audience
Standard Operating Procedure format for Facility Maintenance Services
1.) Title Block:
This section outlines all the details required for the purpose of referencing.
- Self explanatory name of the SOP
- SOP serial number
- SOP revision number
- Name of department for which its being issued
- Date of issue
- Signatures of the management
2.) Table of contents and numbering format:
SOPs that are longer need to be broken down into smaller sections for better clarity. These sections can be divided into headings and numbered subsections.
3.) Definitions:
This outlines the meaning of all acronyms, abbreviations, terms and concepts the readers need to know.
4.) Purpose:
The purpose section should include the reason a certain SOP is being created. It should also mention who is the target audience and what would be the consequences of not following the SOP.
5.) Scope:
This section defines what the SOP covers and what is not a part of it. Some SOPs might involve a linear process while others may be hierarchical processes involving several steps.
6.) Responsibilities:
Make a list of all the personnel and departments who need to be aware of these SOPs while performing their work.
7.) Health and Safety:
Outline any health and safety procedures that are to be followed. This includes risks to be vigilant about and any warning that may apply.
8.) Procedures:
Provide step-by-step instructions on how to follow the SOPs. For time dependent SOPs, identify when a procedure needs to be carried out. For information dependent SOPs, identify the source that needs to be referred to. Add process flowcharts and checklists where needed.
9.) Quality control and quality assurance:
List activities that need to be carried out to ensure the task is carried out as desired.
10.) Reference section:
Any manuals, illustrations, additional literature or references of citations need to go in this section.
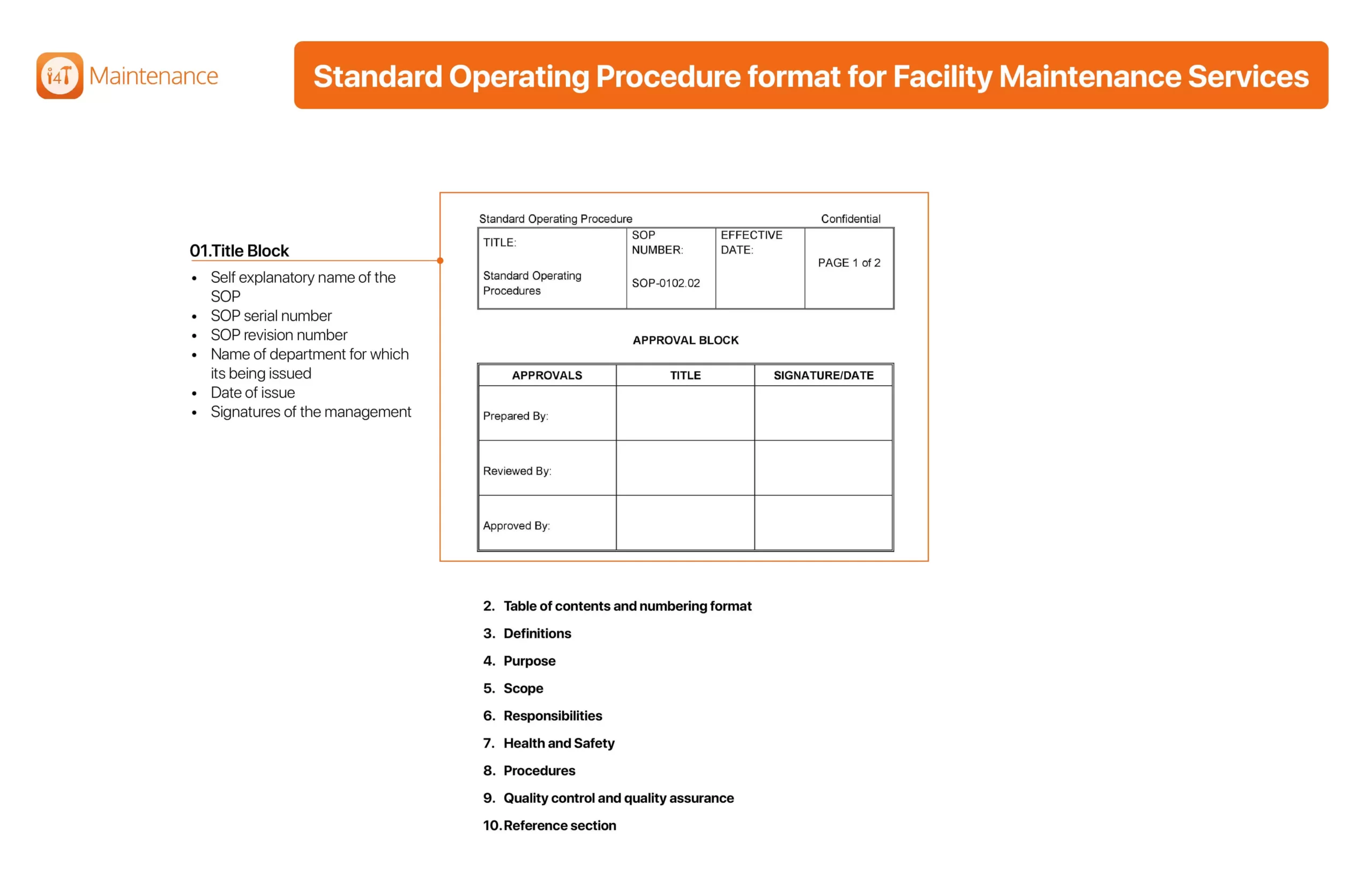
Which Facility maintenance processes require SOPs
SOPs outlining the method of operating are ideal for routine and repetitive tasks as opposed to those that require critical decision making or problem solving.
Some of the maintenance processes that require management to create SOPs include:
- Deferred Maintenance Tasks
- Preventive Maintenance Scheduling
- Routine asset inspections by Facilities Maintenance Services Suppliers
- Work Authorisation
- Data input into a Computerised Maintenance Management System (CMMS)
- Creating, managing and completing work orders
- Inventory procurement and management
- Assigning routine maintenance tasks
Industries that are using facility maintenance SOPs
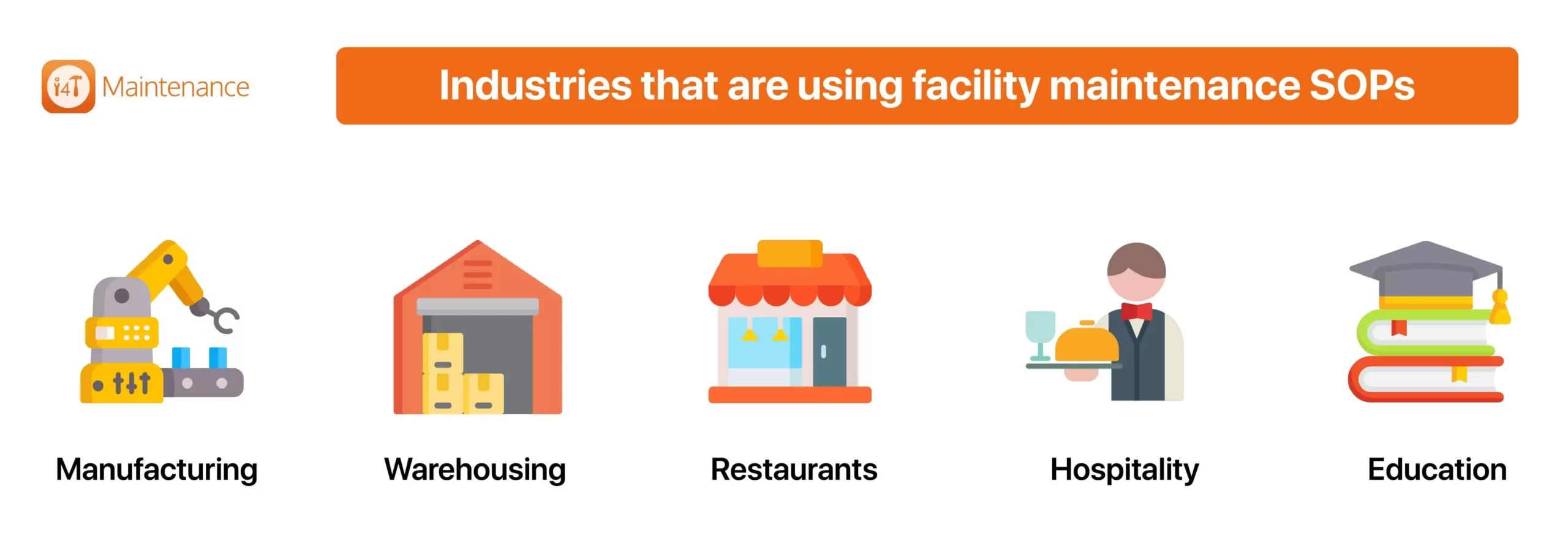
Manufacturing
Manufacturing facilities need to abide by a number of state and federal laws including equipment safety and health and environmental rules and regulations.
Facility managers, operational staff and maintenance teams need to ensure quality control standards are being met and being continuously improved. These SOPs not just help with asset management but ensure products reach the market at the right time. This is done by minimising downtimes and process inefficiencies.
Warehousing
Restaurants
SOPs play a huge role in training new staff joining the kitchen. They are also vital to maintaining food quality and safety, keeping appliances running smoothly and serving the guests.
SOPs for staff hygiene, cleaning equipment used for food preparation and menu production are vital to keep customers coming back.
The fast-paced nature of the restaurant industry requires that SOPs are fully understood top to bottom. It leaves no room for going back to manual folders for cross checking. Digitised SOPs come into play here that keep all guidelines on the fingertips of every staff member.
Hospitality
A positive guest experience is dependent on how well the building maintenance is carried out. In property maintenance SOPs play a vital role. Common tasks include HVAC maintenance, plumbing, electrical, sanitation, guest safety, equipment, supplies, furniture and space requirements.
More specifically, facility maintenance managers need to look closely at matters such as:
- Facility evacuation and lockdown under emergencies
- Housekeeping and cleaning
- Laundry and kitchen operations
- Building safety
Education
Facility management for schools needs to ensure day-to-day operations are running smoothly. It also focuses on meeting long term school priorities. Heavy use of facilities by children calls for routine preventative maintenance and handling repair demand on an emergency basis.
SOP forms and checklists to maintain school buses, buildings and grounds, food service, sanitation, fire and water safety all play an important role.
With the right SOPs in place, facility maintenance services managers are able to provide a conducive environment for teaching and learning round the year.
Wrapping up
Every industry has its own specific SOPs to keep workflows and quality in check. For your Maintenance SOP document to serve its desired purpose effectively, it is important to take the input of all stakeholders into consideration. This is especially true for workers who will be actually performing the work. The true value of SOP lies in the fact that it speeds up the process of teaching new employees how to carry out their responsibilities in accordance with the set rules.
When implemented the right way, SOPs serve as the best way to ensure quality of maintenance work done. It also provides safety for occupants, ensures legal compliance, eliminates miscommunication, enhances efficiency and avoids mistakes.
Maintenance software such as i4T Maintenance, can help you implement your SOPs effectively for companies offering facilities maintenance services. Signup today and transform the way you work.
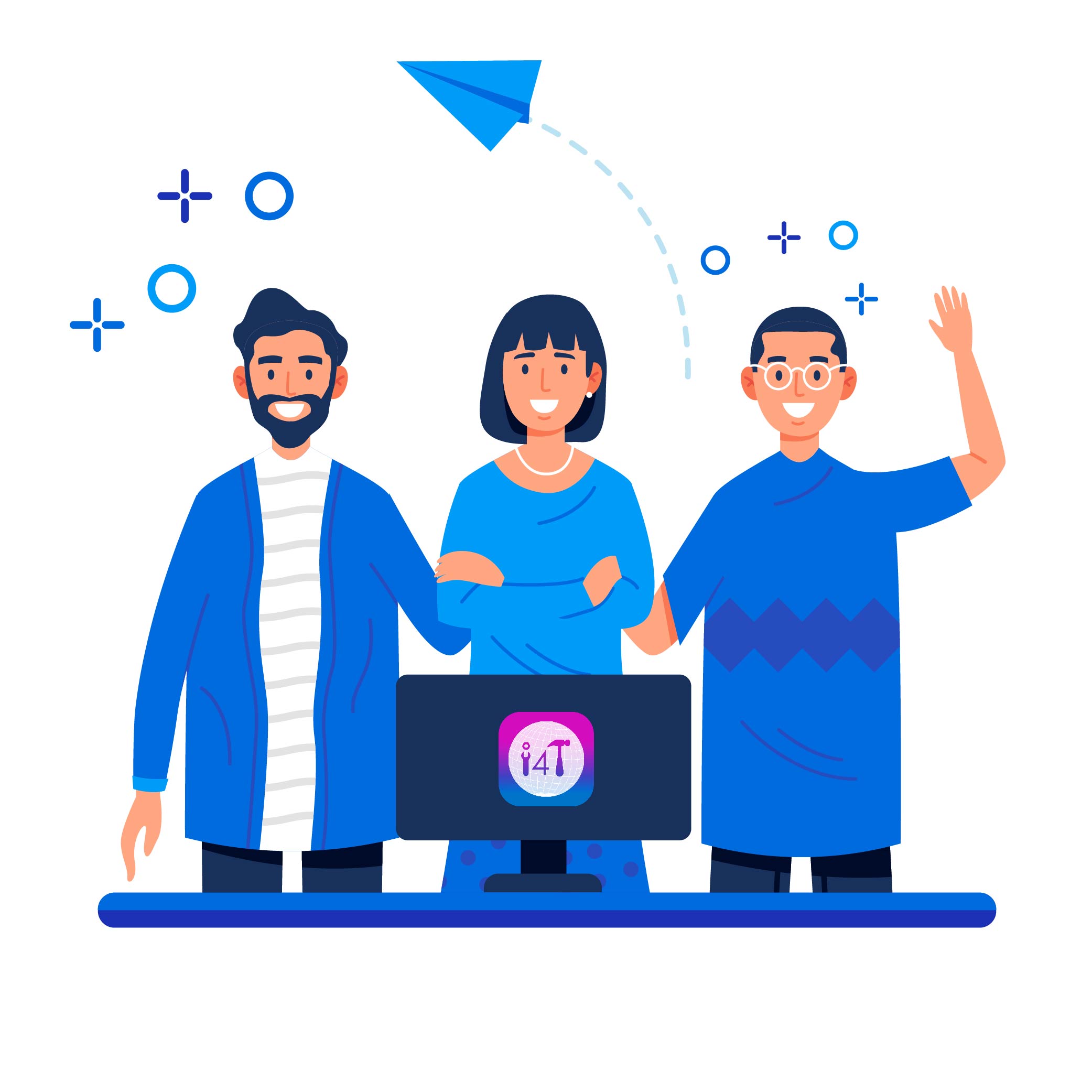