Prescriptive maintenance is, by far, the most comprehensive and high-level maintenance method. It is rapidly gaining popularity among maintenance professionals as well as operational staff.
It’s important to note that prescriptive maintenance approach is not as widely utilised as one might think given its benefits. However, that can be solely attributed to the fact that many industries are yet to achieve predictive maintenance to begin with.
Let’s delve deeper into the importance of prescriptive maintenance and how it differs from predictive maintenance. We’ll also briefly try to explain what steps are involved in the process. Lastly, we’ll take a look at some of the examples of prescriptive maintenance from the real world.
What is prescriptive maintenance?
Prescriptive Maintenance, also known as RxM, is a specialised asset maintenance technique to reduce operational risks. It follows the process of collecting and analysing data about the condition of an asset. It then provides recommendations to avoid a certain risk in the future.
Prescriptive maintenance utilises machine learning (ML) and artificial intelligence (AI) to modify operational conditions to achieve a desired outcome. It also helps with intelligent planning and scheduling of asset maintenance based on analytics.
Difference between prescriptive maintenance and predictive maintenance
Anyone who has come across both of these terms will find a striking similarity between the two.
The difference lies in the course of action and the outcomes of both.
Predicting vs Prescribing
Predictive maintenance aka PdM, analyses data collected from an asset such as certain machinery or equipment. This helps in understanding the exact operational patterns, identify possible risks, and predict when a failure will take place.
Vibration analysis, for instance, can detect that a failure is about to occur as much as 3 months in advance. However, it still needs a level of human intervention. Managers need to analyse the data and decide what course of action needs to be taken. They then create a work order and assign it to a technician.
Prescriptive maintenance, on the other hand, goes a step further, doing all of the manager’s work automatically. It not only collects the data, predicts the pattern but also suggests a recommended action. It then creates a work order and assigns it to the technician.
This virtually eliminates any human intervention.This translates into a more comprehensive approach and a highly streamlined workflow.
Avoiding vs Delaying
Predictive maintenance identifies a certain risk that needs to be addressed. Prescriptive maintenance, on the other hand, runs a series of ‘what if’ scenarios using historically collected data patterns.
For example, Prescriptive Maintenance may recommend that by reducing the speed to half, it will double the time to asset failure.
Both predictive and prescriptive models have their own benefits. Choosing them is largely based on your company’s specific requirements and scenarios.
Benefits and drawbacks of Prescriptive Maintenance
While prescriptive maintenance is quickly gaining popularity due to its ability to eliminate human intervention altogether, it does have its limitations.
Let’s briefly go through some of the pros and cons this asset maintenance technique has. This will help you decide if this approach is right for your business.
Benefits of Prescriptive Maintenance | Barriers to implementation of RxM |
Draws data by creating multiple ‘what if’ scenarios using ML and AI and prescribing an outcome for each. | High cost of retrofitting equipment with sensors and Artificial Intelligence and Machine Learning capabilities. |
Is able to run a cost/benefit analysis of the proposed course of actions. | Regulations governing the operations might hinder managers to take actions on the suggestions provided by prescriptive maintenance. |
Offers the most advanced way to optimise operational efficiency and reduce downtime. | It can take time for the system to become useful, as prescriptions are made based on historical data analysis. |
Assist with important capital expenditure decisions using simulations of future enhancements or upgrades on digital models of equipment. | Organisational culture might stop the system from being implemented across all operational levels. |
Helps make recommendations to solve highly complex equipment issues. | Prescriptive maintenance technique is relatively new. Facility maintenance managers still don’t have full confidence in its ability to suggest solutions. Especially so for safety critical equipment that requires human intervention. |
Prescriptive Maintenance Workflow
- Description: What happened?
- Diagnosis: Why did it happen?
- Prediction: What will happen?
- Prescription: What to do when something happens?
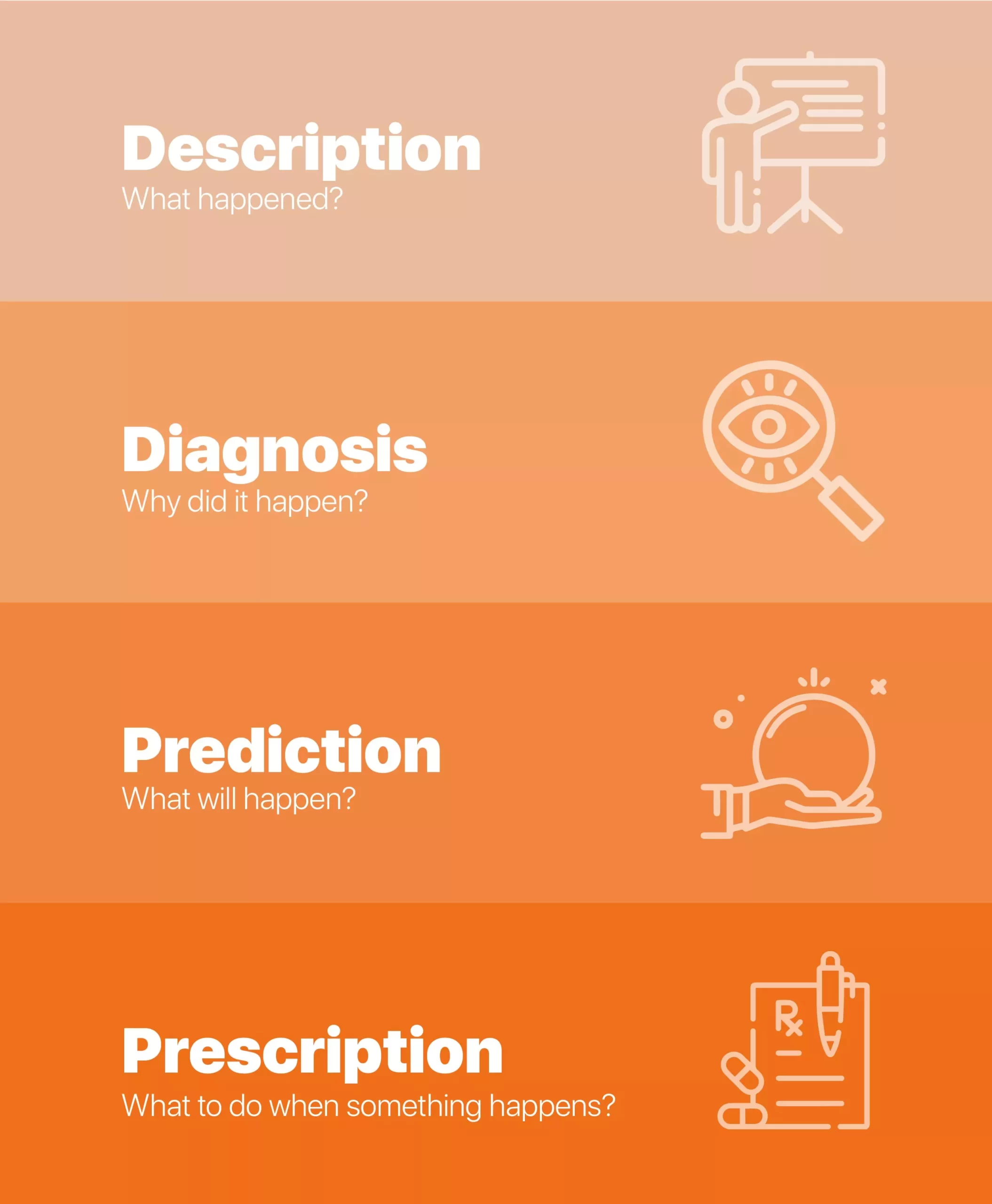
Carrying out prescriptive maintenance - a Step by Step approach
1. Planning the implementation
2. Historical data collection
3. Carry out FMECA
4. Install sensors and software to capture data
5. Setting up the algorithm
- Recommendations and instructions from equipment manufacturers.
- Past data stored digitally or in print.
- Data collected from real-time sensors
- Data collecting from non-destructive testing
6. Incorporate prescriptive maintenance actions
7. Roll out your prescriptive maintenance program and let it improve over time
8. Get a buy-in from all stakeholders
Your prescriptive maintenance program is only as good as the people involved in getting it up and running. Internal resistance to change might hinder you from reaping its full potential. For all parties to accept the new way forward, an organisation-wide change management program is required.
Examples of prescriptive maintenance
The maintenance and reliability best practices have only improved over the years with the right technology to help them out.
Today, there are several industries that have realised the benefits of Prescriptive Maintenance. These companies are excelling in terms of reduced maintenance costs, higher workplace safety and increased revenues.
Let’s see how RxM is being implemented by various industries to improve operational efficiency at industrial plants.
Below are a few examples from the real world.
RxM in Chemical Industry
A European chemicals producer was experiencing repeat failures of their hyper compressor. This resulted in equipment downtime and very high maintenance costs on a frequent basis.
Their maintenance team decided to implement Prescriptive Maintenance having Machine Learning and prescriptive analysis capabilities. This was done after carrying out a pilot program for a hyper compressor that was critical to their business operations.
This helped their maintenance teams get advance warnings of the failures about four weeks before they occurred. It has given them plenty of time to take corrective measures.
RxM in Mining
A global mining company, handling iron ore, was in need to predict and avoid failures in its material transport operations. The company already had telematics data on faulty wheels, wheel bearings, and axles coming from their rail cars.
Using prescriptive maintenance, the company began getting advance notice of upcoming issues. Not only this, but it is also getting prescriptive alerts as much as 4 weeks in advance.
This allowed them to proactively handle the maintenance of their transport system. The mining company is now able to significantly cut down their downtime by avoiding rail car failure.
RxM in Cement Manufacturing
A cement plant was experiencing frequent cyclone blockages in its Kilns resulting in higher unplanned downtime and maintenance costs.
By utilising predictive maintenance and prescriptive maintenance, they were able to make use of Machine Learning capabilities on past blockages. It helped them to identify failure signs and recognise the pattern.
This helped them understand the root cause of the problem. Not only this, but they also obtained prescriptive guidelines on optimising maintenance and taking action several days in advance.
Final Thoughts
Without a doubt, Prescriptive Maintenance is the future of property maintenance management. When implemented correctly, Prescriptive Maintenance methods to asset management results in:
- Reduction in asset failure or unplanned downtimes
- Slashed technical maintenance costs
- Optimised operations and streamlined processes
- Longer lifespan of assets
- Frees up managerial staff as it requires little human intervention
- More accurate financial decision making
Finally, it’s important to note that it may not be ideal for all industries to implement it. Especially the ones that are still struggling with less complex maintenance techniques.
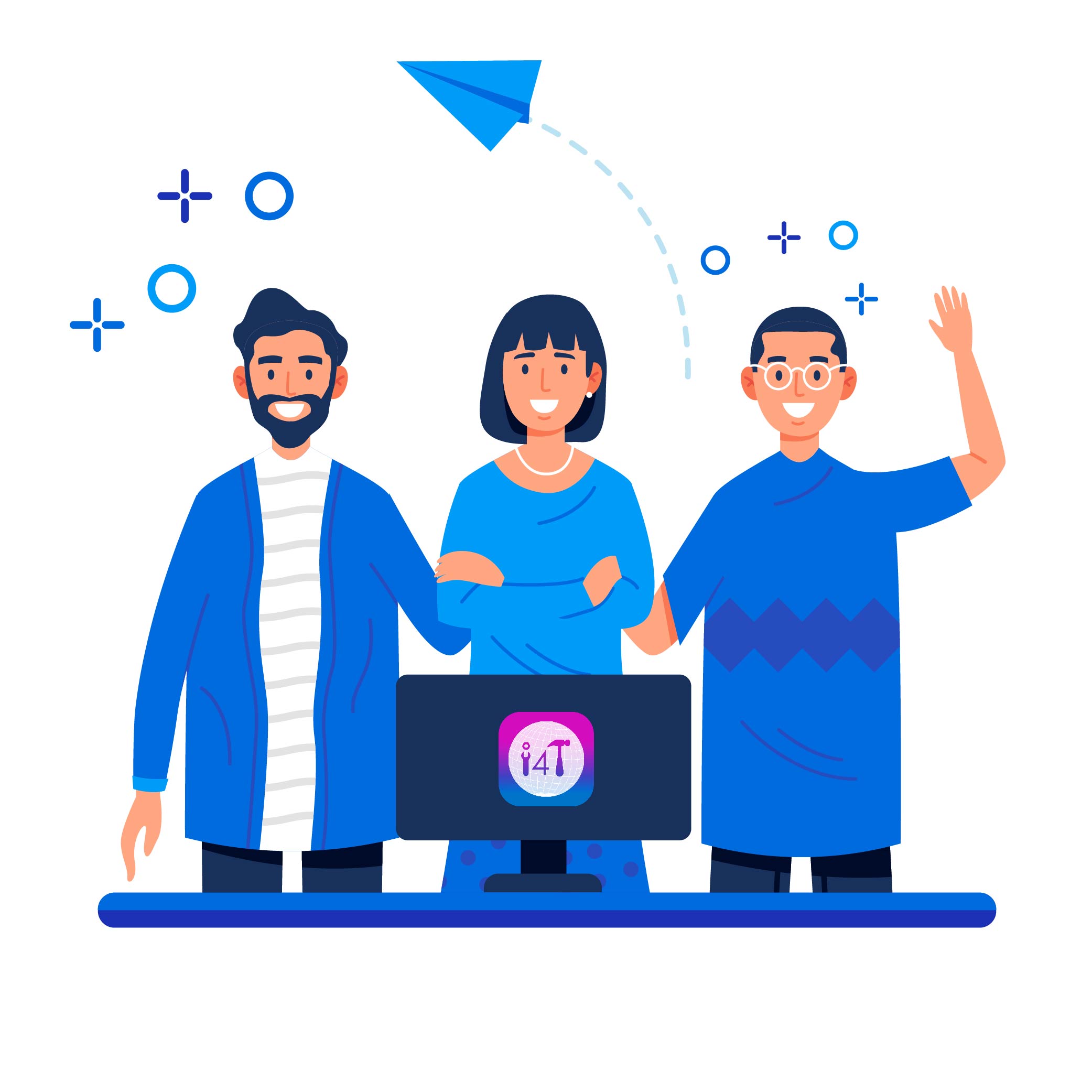