The key to running a great facility lies with good planning. Therefore, the backbone of any maintenance management team is a well managed schedule.
Scheduled maintenance requires managers to find the best time to carry out a work order. They then assign a technician that is best qualified to carry it out.
When done correctly, scheduled maintenance ensures the facility is running optimally round the year.
Let’s dive deeper into the topic and learn more about how your facility can benefit from scheduled maintenance.
What is Scheduled Maintenance and What Does a Maintenance Scheduler Do?
Scheduled maintenance is any inspection, repair or maintenance work that is planned in advance. It has a set deadline and is assigned to a technician. It is carried out to take care of regular wear and tear of a piece of equipment or system.
In order to simplify the scheduled maintenance workflow, facility owners have specific positions to fill in the role of a maintenance scheduler.
This individual is responsible for creating a maintenance plan. He/she will also bring all the resources together that are required to complete a work order.
The responsibilities of a maintenance scheduler include organising and coordinating personnel, materials, resources and access to assets. More specifically, maintenance schedulers:
- Coordinate with other departments to ensure timely availability of resources, materials and personnel.
- Monitoring equipment performance to identify issues before they turn into bigger problems.
- Create and manage schedules for technicians to carry out maintenance work orders.
- Ensuring guidelines and SOPs are followed at every step of the process.
- Review work orders to determine additional resources or time needed to complete them.
- Keeping a record of maintenance activities for each work order.
- Scheduling repair work for internal staff and coordinating with subcontractors.
- Regularly carrying out training programs to ensure technicians are well-versed in carrying out the work.
Today, technology platforms like i4T Maintenance are replacing the need for a dedicated maintenance scheduler. It automates nearly all of the tasks that were traditionally done by maintenance personnel.
Scheduled Maintenance Workflow
Scheduled maintenance is carried out at specific times of the year. It can take the form of a recurring work order. An example could be changing the filters of an air conditioner in April and October. Alternatively, it could be a one-time work order, based on the maintenance need identified through a routine inspection.
It can be prompted through several kinds of maintenance techniques, such as preventive, routine, reactive, or predictive maintenance.
Once the time is decided to carry out the maintenance work, the second step is to determine who will carry it out. How much time is needed to do the job and whether a technician is available are also factored in.
After ensuring that all resources needed to complete the work order are available, the maintenance job is scheduled.
How Scheduled Maintenance Decreases Downtime
The most important goal of carrying out scheduled maintenance is to reduce reactive maintenance, clear maintenance backlogs, and minimise downtime.
Here are some of the ways scheduled maintenance can decrease equipment downtime:
- Scheduled maintenance is similar to regular maintenance carried out on the equipment, ensuring the equipment is always in good working order.
- Scheduled maintenance involves inspection of the equipment, that allows technicians to catch and report problems before they turn into bigger problems.
- Scheduled maintenance carried out over a period of time allows managers to gather vital data on equipment performance. This can help them show trends and schedule maintenance activities based on insights gathered through this process.
- Scheduled maintenance also allows you to carry out maintenance work in times when the equipment is not operational. Hence equipment does not face any downtime due to maintenance work being carried out.
Scheduled Maintenance vs Planned Maintenance
In its most simplistic form, planned maintenance deals with what needs to be done and how it will be done. It begins with the problem and then goes on to determine the process. It also considers resources that are required to carry out that process.
Planned maintenance is the responsibility of a maintenance planner.
Scheduled maintenance, on the other hand, determines when the identified problem can be addressed in the form of a work order. It also determines who will be responsible for carrying out the work.
Scheduled maintenance is the responsibility of a maintenance scheduler.
Scheduled Maintenance vs Preventive Maintenance
Scheduled maintenance and preventive maintenance share the same goal of ensuring the equipment faces minimum downtime and process disruption.
However, while scheduled maintenance considers the time and personnel carrying out the maintenance task, preventive maintenance takes into consideration advanced analytics and diagnostic capabilities that ensure that an issue never takes place in the first place.
Togather, scheduled maintenance and preventive maintenance can increase a systems uptime and efficiency while reducing costs associated with failures.
What Does SMCP (Scheduled Maintenance Critical Percent) Mean for Maintenance?
No matter how efficiently you have scheduled your maintenance work orders, sometimes unforeseen circumstances cause you to miss your set deadlines.
With the use of a SMCP, maintenance managers are able to determine which of these planned recurring work orders are overdue. It then determines how they need to be prioritised in terms of completion.
This is done by calculating by how much time these scheduled work orders are overdue. The higher this percentage, the more priority is given to it.
How to Calculate SMCP?
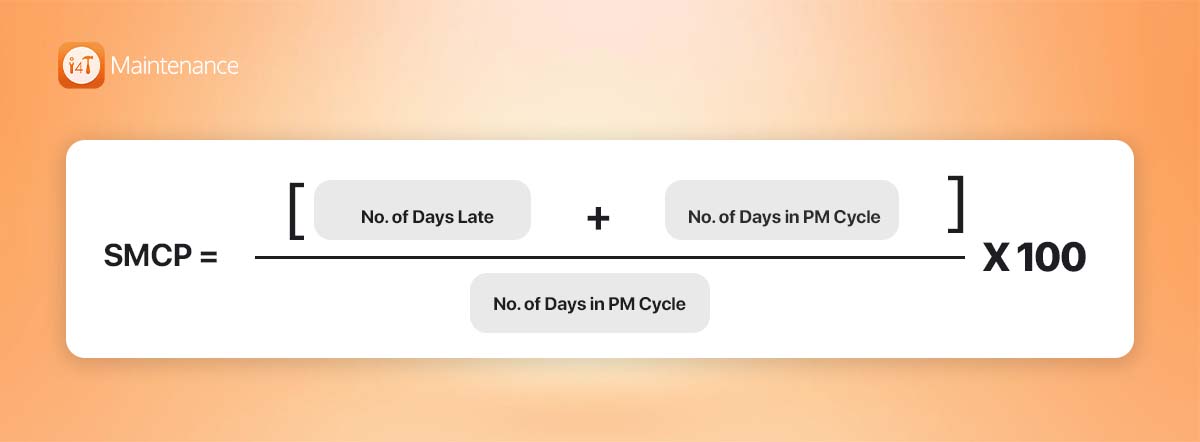
How Do I Create a Maintenance Schedule?
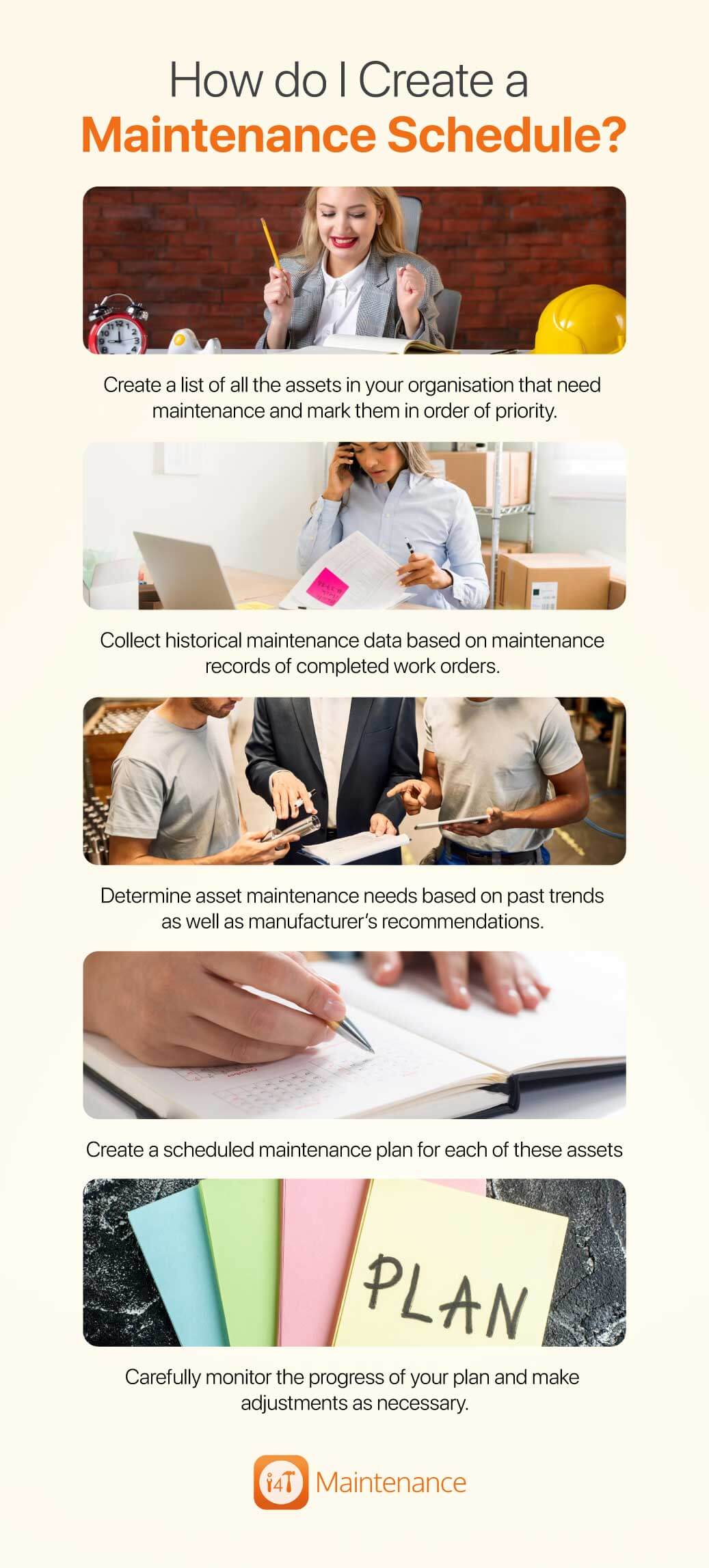
Benefits of Scheduled Maintenance
We have already established that scheduled maintenance reduces the equipment downtime and failure. However, it can benefit organisations in many more ways. Let’s look at some of the reasons why carrying out scheduled maintenance is important for your business.
- Scheduled maintenance is all about ensuring the right person completes the job at the right time. Hence, it plays a vital role in maximising worker productivity or personnel utilisation.
- It helps add more years to the life of an asset. This means there will be less equipment replacements and costs will be saved in purchasing new equipment.
- The overall maintenance costs are reduced since maintenance is carried out as per schedule. This means there will be fewer breakdowns and it will cost less in emergency repairs or reactive maintenance.
- Tasks are handled proactively and maximum number of work orders are completed. This means overall efficiency of the organisation is enhanced.
- The liability of the asset is reduced since the asset is always kept in safe working condition for those handling it.
What are the Types of Scheduled Maintenance?
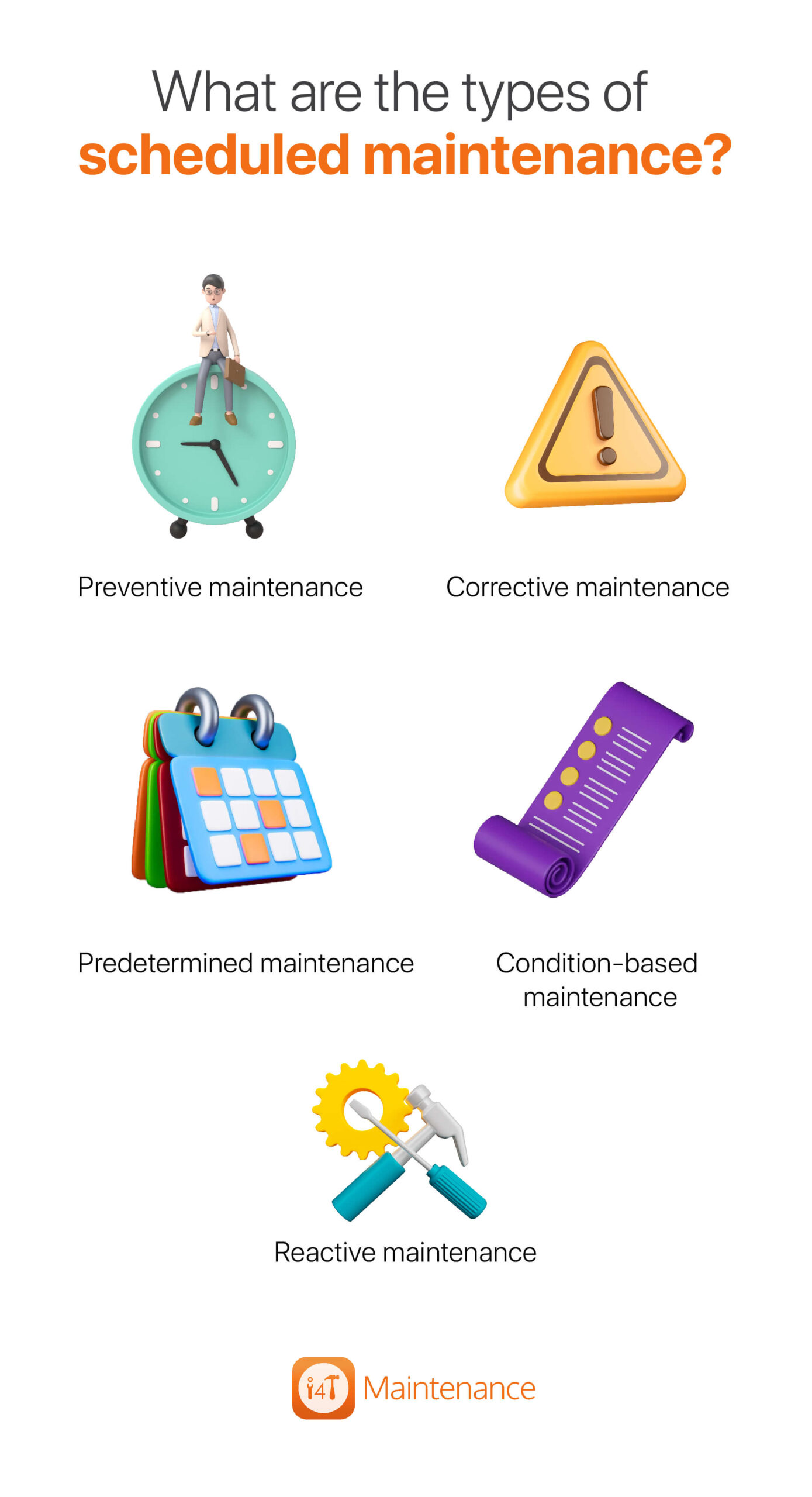
- Preventive maintenance: This is based on a regular or periodic time-based schedule.
- Corrective maintenance: This is a one-off maintenance and is scheduled based on when an error is identified.
- Predetermined maintenance: This is when you follow the manufacturer’s recommended maintenance schedule to upkeep your assets.
- Condition-based maintenance: This maintenance is scheduled when a specific condition is reached.
- Predictive maintenance: This is data driven maintenance based on present parameters.
- Reactive maintenance: Similar to corrective maintenance, maintenance is scheduled when an asset breakdown occurs.
What are the Types of Scheduled Maintenance?
Your scheduled maintenance program is only as effective as the communication strategy that accompanies it.
The scheduled maintenance messaging needs to flow seamlessly between facilities managers, technicians and other stakeholders.
In order for your massages to be understood clearly you need to make sure:
- Everyone understands the importance of the task at hand and what it entails. Everything from what work will be interrupted, who will be impacted and how long it will take needs to be communicated.
- Sufficient notice is given to all the parties involved from technicians to those whose work will be impacted.
- The right channel is used so no one is left out from being informed.
- The message involves all the necessary details. Who will be performing the work; who to contact in case of queries and concerns; and an alternate way to avoid disruptions if possible.
Ensure your scheduled maintenance message sounds friendly and empathetic, rather than robotic and cold.
Adopting CMMS for Scheduled Maintenance
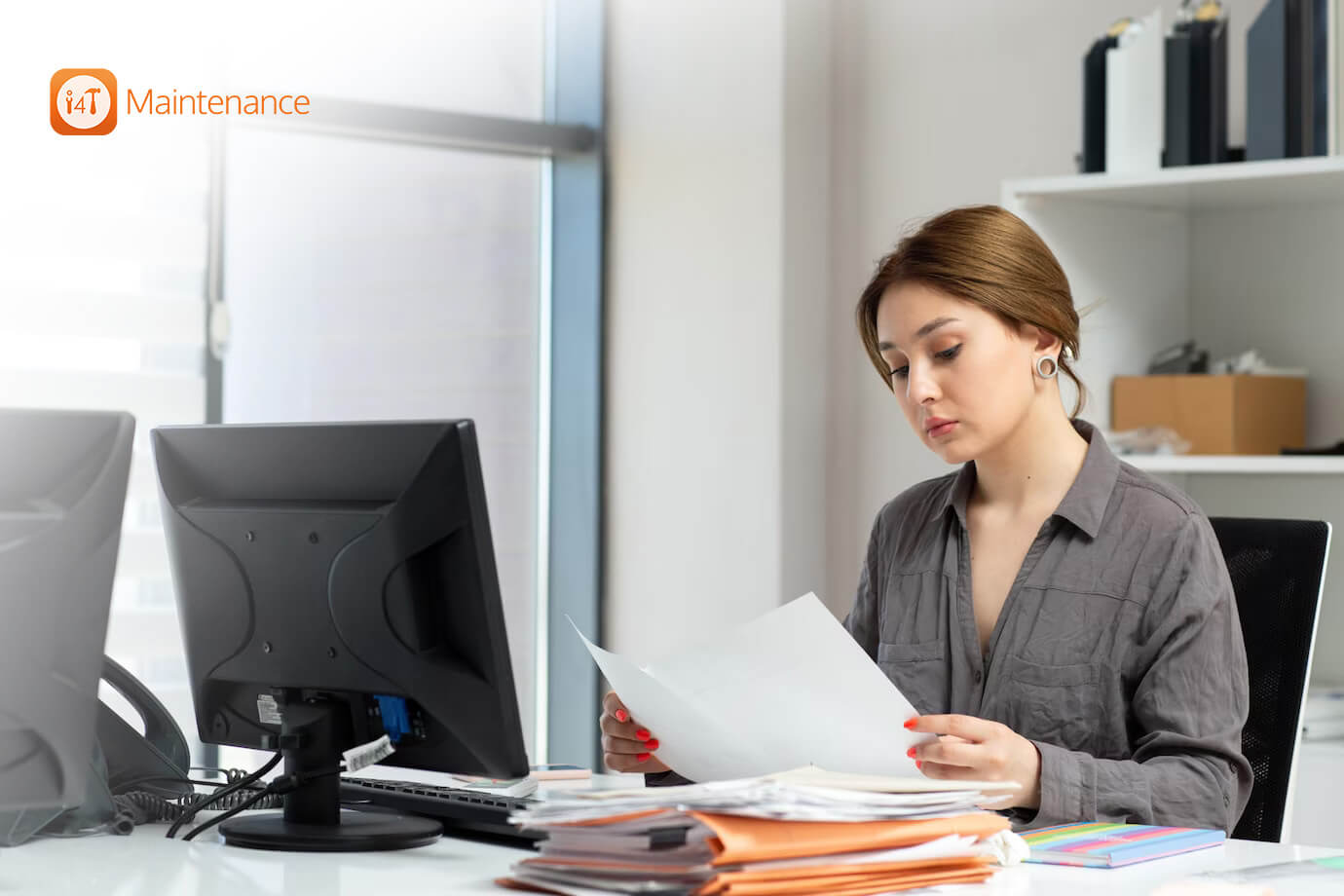
A robust scheduled maintenance program is the backbone of any great facility. This holds true, irrespective of its size and the complexity of its operations.
In order to minimise maintenance errors, optimise resources and avoid costly repairs, automating scheduled maintenance can help. Hence, choosing the right CMMS is very important.
With i4T Maintenance, maintenance managers can easily connect to certified field service technicians via i4T Business. They can schedule maintenance work orders, track progress of work in real-time and get valuable insights for vital decision making through historical record keeping.
Ready to start optimising scheduled maintenance for your facility with i4T Maintenance? Register today and get started!
Hot off the press!
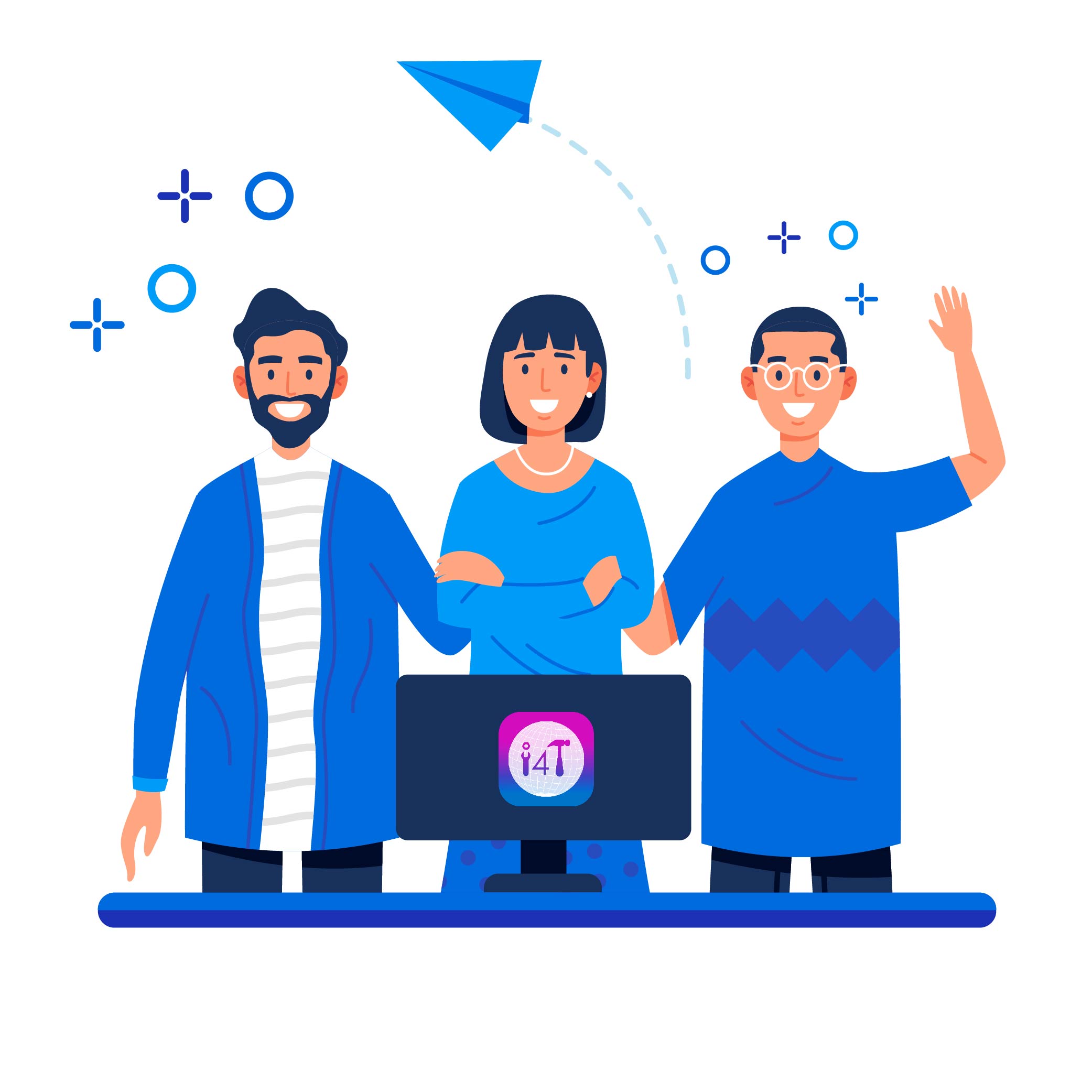
With our cutting-edge technology and in-depth knowledge of how the Field Service Management sector operates, the i4T Global Team loves to share industry insights to help streamline your business processes and generate new leads. We are driven by innovation and are passionate about delivering solutions that are transparent, compliant, efficient and safe for all stakeholders and across all touch points.