Establishing a streamlined workflow for maintenance orders is not simple. While it’s easy to process a couple of orders, you can soon find yourself struggling for control as you try to handle multiple orders at a time.
Before you know it, your work orders are all over the place and your process is plagued with inefficiencies at every step of the way.
Here we will talk about how to effectively manage your work orders, how the order management system works and why you should use a work order management software to improve workflow.
What is work order management and how does it ensure maintenance of properties.
Effective work order management process enables teams to move from point A to point B without any bottlenecks and delays so maintenance issues are resolved on time.
What is work order lifecycle
Work order life cycle entails the three phases of the work order which are work order creation, completion and recording.
These phases can also be defined as the work order management process flow and can be further divided into 6 steps including everything from task identification, work order creation, prioritizing and scheduling, assigning and completing, closing and recording and finally reporting or analyzing.
Work order management steps:
1.) Identifying an issue:
This step involves identifying the issue and setting the process in motion to take action and fix it.
2.) Work order creation:
Creating a work order involves mentioning all the details of a given maintenance issue along with photos/videos and any other information.
3.) Prioritizing and scheduling:
Since there may be a number of work orders in your list, prioritizing and scheduling tasks based on how critical they are, is a must.
4.) Assigning and completing:
By this step you are ready to assign the work order to the resource best fit to perform it. They will carry out the work order and complete it as required.
5.) Closing and recording:
Once all the requirements of the work order are fulfilled, it’s now ready to be closed and the manager can document the details to be reviewed later.
6.) Analyzing the work order:
This is the time for you to generate a report of the closed work order and analyze the valuable information it contains. This information gives you crucial insights into your assets and help you make vital decisions for future maintenance.
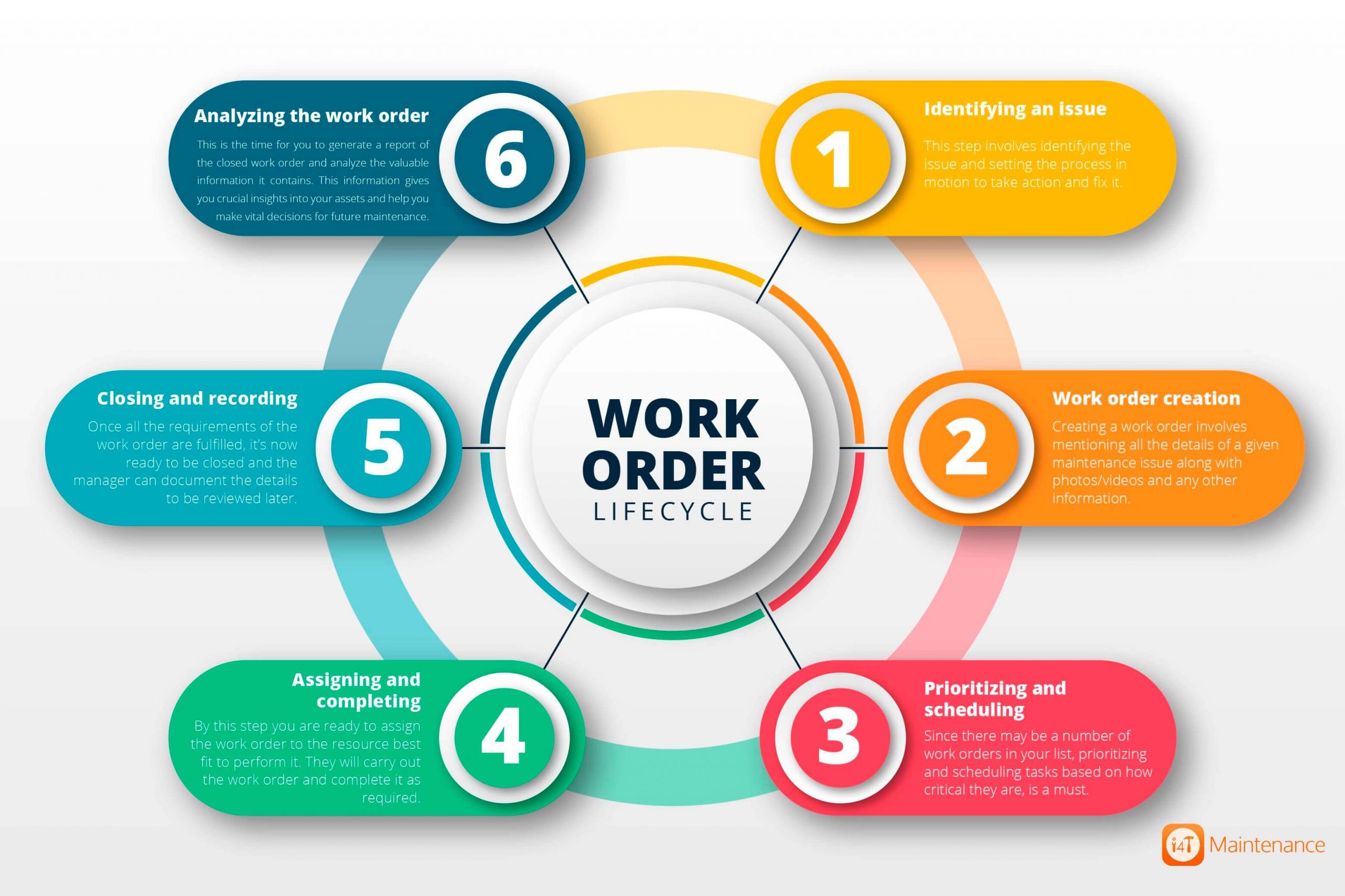
What are the types of work orders
Maintenance work orders fall into the following categories:
1.) General work orders:
General work orders are all those orders that are not preventative, inspection, emergency or corrective work orders. These are the day to day work for tasks such as installations, painting a building and so on.
2.) Preventive maintenance work orders:
This is scheduled maintenance that has to be carried out on a regular basis in order to avoid asset breakdowns that may result in downtime. This includes making checklists for tasks and requirement to be ticked off.
Read: What is Preventive Maintenance? A Complete Guide to Preventive Maintenance
3.) Inspection work orders:
This kind of work order requires inspection to be carried to audit the condition of an asset and to identify a problem. If a problem is detected a separate work order is created to take corrective action.
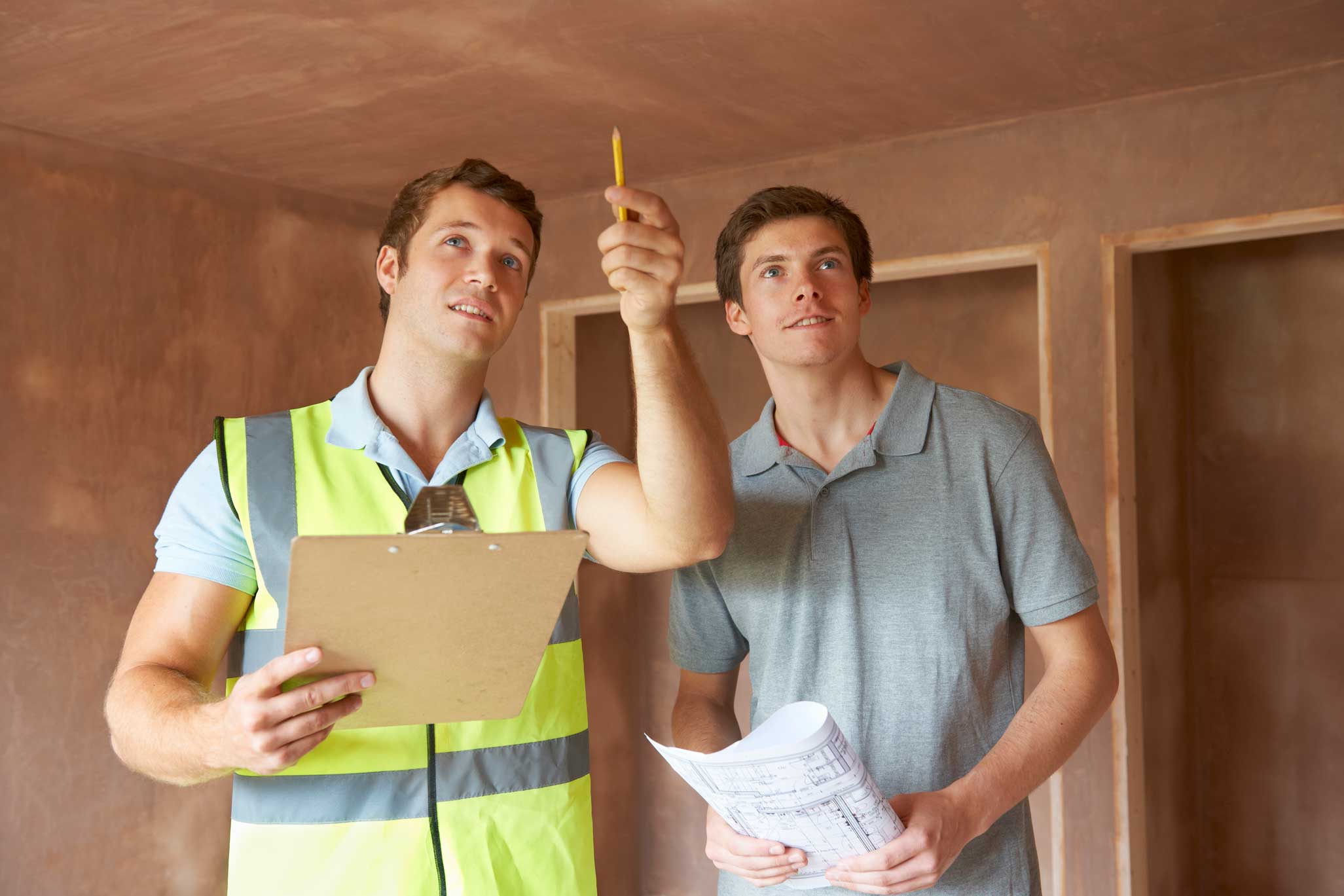
4.) Emergency work orders:
Emergency work orders are created when assets break down unexpectedly and need to be taken care of on an urgent basis. This kind of work order calls for reactive maintenance and requires the technician to note down the details of the breakdown in order to avoid such failures in the future.
5.) Corrective maintenance work orders:
Issues that show up during preventive maintenance are resolved under corrective maintenance work orders. As the name suggests, corrective maintenance is carried out to fix issues that cause the assets to have glitches.
What are the benefits of a work order system
A work order system empowers maintenance teams to streamline workflows, eliminate errors, reduce processing time and maintain records.
Here are 4 main benefits of a work order maintenance management system for businesses of all shapes and sizes.
1.) One hub for all work orders
With multiple work orders it is not uncommon for duplications, incorrect data entries, information all over the place and other inefficiencies. With a central system for all your work orders, not only will your teams be on the same page but it also eliminates errors and helps you run your business more efficiently.
2.) More control over information access
Work order management systems allow managers to provide information access to users based on their role in the organization. While some users can only view information, others can change it. This helps in accountability and improved performance.
3.) Real-time process tracking
One of the best things about work order management systems is that they allow you to track changes as they happen. This ensures that you never run out of inventory and take instant action on service delivery bottlenecks enhancing quality, lowering costs and improving efficiencies.
5.) Record keeping
By automatically recording every work order, management has better insights into every aspect of the workflows and is able to make better budgeting and planning decisions for the future.
Work order management tips for property managers
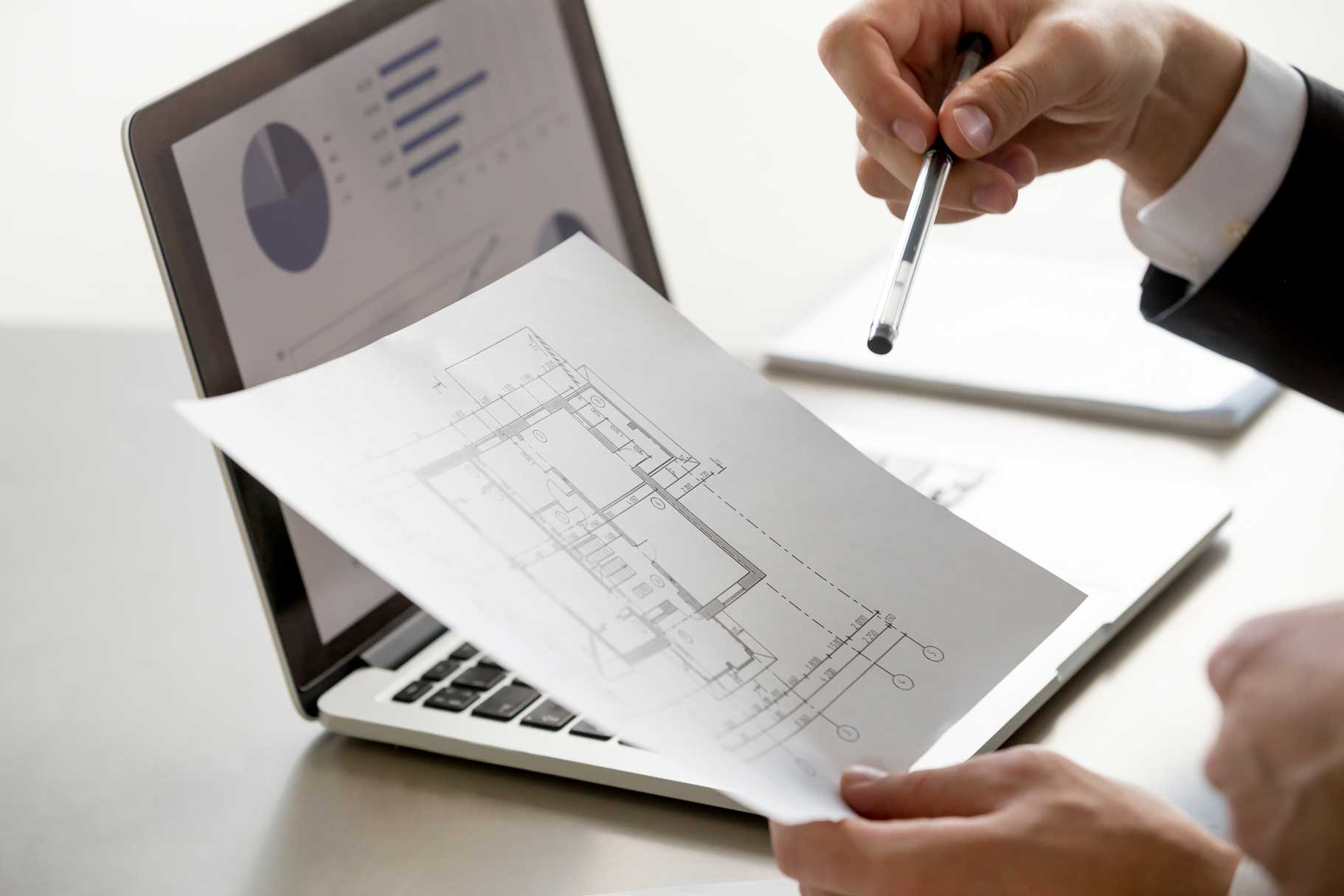
Here are some tips to save the day for property managers:
1.) Simplify placing work order requests
A lot of work orders are not completed on time just because the property managers are clueless when the order was placed and where it lies in priority. Consider using a Work Order Management System that helps simplify the process of how property occupants place orders. From the same platform you can assign and schedule work and track progress.
2.) Plan ahead
Property managers are often juggling between seasonal work, day to day service requests and emergency call outs. The best way to handle all the work flow is to plan ahead. Make sure you have set up contractors well in advance and have a cushion in case you need to add more projects to your list by a given date.
3.) Focus on preventive maintenance
Look out for tasks that can be attended today so they won’t cause problems later on.
Preventive maintenance helps keeping problems from piling up and turning into bigger headaches.
This is also a good way to keep your properties in good shape and save time and frustration in the long run.
4.) Keep a list of trusted field service suppliers handy
Once you find a good Field Service Supplier, do not lose them!
As a property manager, your trusted field service suppliers should be available round the clock and deliver quality work every time.
Make sure they are licensed, insured and background-checked.
Once your list is ready, you can relax that you won’t have to scramble looking for a supplier the next time an emergency work order comes up.
How work order management system can help you save time and money
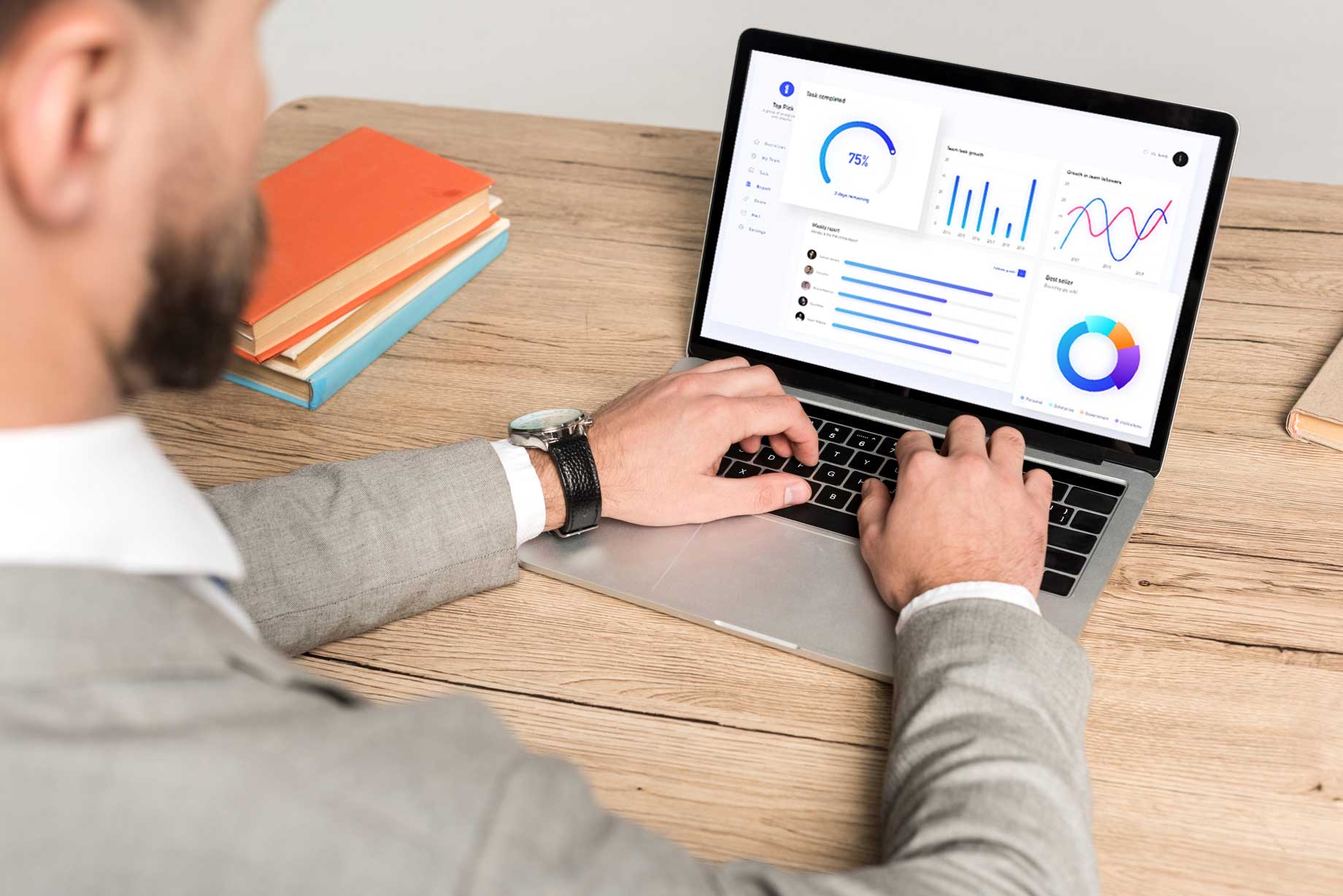
Since all these tasks are automated by the system itself, it not only reduces errors of duplication and incorrect information but also speeds up the entire process by eliminating unnecessary hold ups such as accessing information regarding the order and getting confirmations.
This helps property managers spend more time on resolving a problem rather than independently overviewing each process.
Processing orders quickly, eliminating errors and guesswork and avoiding non-compliance fees by complying with regulations all help in building a great rapport for the business and saving money.
Work order management best practices
Work order management systems are only as good as the people using them. While the system will do most of the heavy-lifting for you, there are a few things that need to be done on the part of the property managers as well.
Here are some work order management best practices that maintenance teams or property managers should never ignore:
- Ensure a maintenance request has been formally submitted before you create the work order and proceed with it.
- Give permission to approve service requests only to certain staff members. This ensures only valid requests with enough information reach the maintenance teams.
- Prioritize the work order based on not just the severity of the service request but also the current workload.
- When scheduling the work order, consider where it lies on the priority table and how it will be followed up.
- Fill in the missing information regarding assets, location, documentation and other notes when assigning the work order.
- Document everything as it happens.
While it may seem a tedious task, records are one of the most powerful arsenal to handle disputes internally as well as externally.
Work order software vs CMMS software
A work order is an important part of any maintenance management software. It helps maintenance managers to receive service request, assign work orders and help them complete in a timely manner.
However, a CMMS (computerized maintenance management system) software goes beyond just a simple work order management system and incorporates many other features including team scheduling, handling maintenance protocols, tracking assets, controlling inventory, overlooking budgets, analyzing reports and monitoring performance.
Wrapping up
Work order management software cuts down workflow process time, reduces emergency requests with effective preventive maintenance, decreases tedious tasks, extends asset life span and gives you a deeper understanding on your assets based on valuable business intelligence.
Work order systems help your business to run efficiently with smoother workflows and help your teams deliver an exceptional maintenance service experience.
Hot off the press!
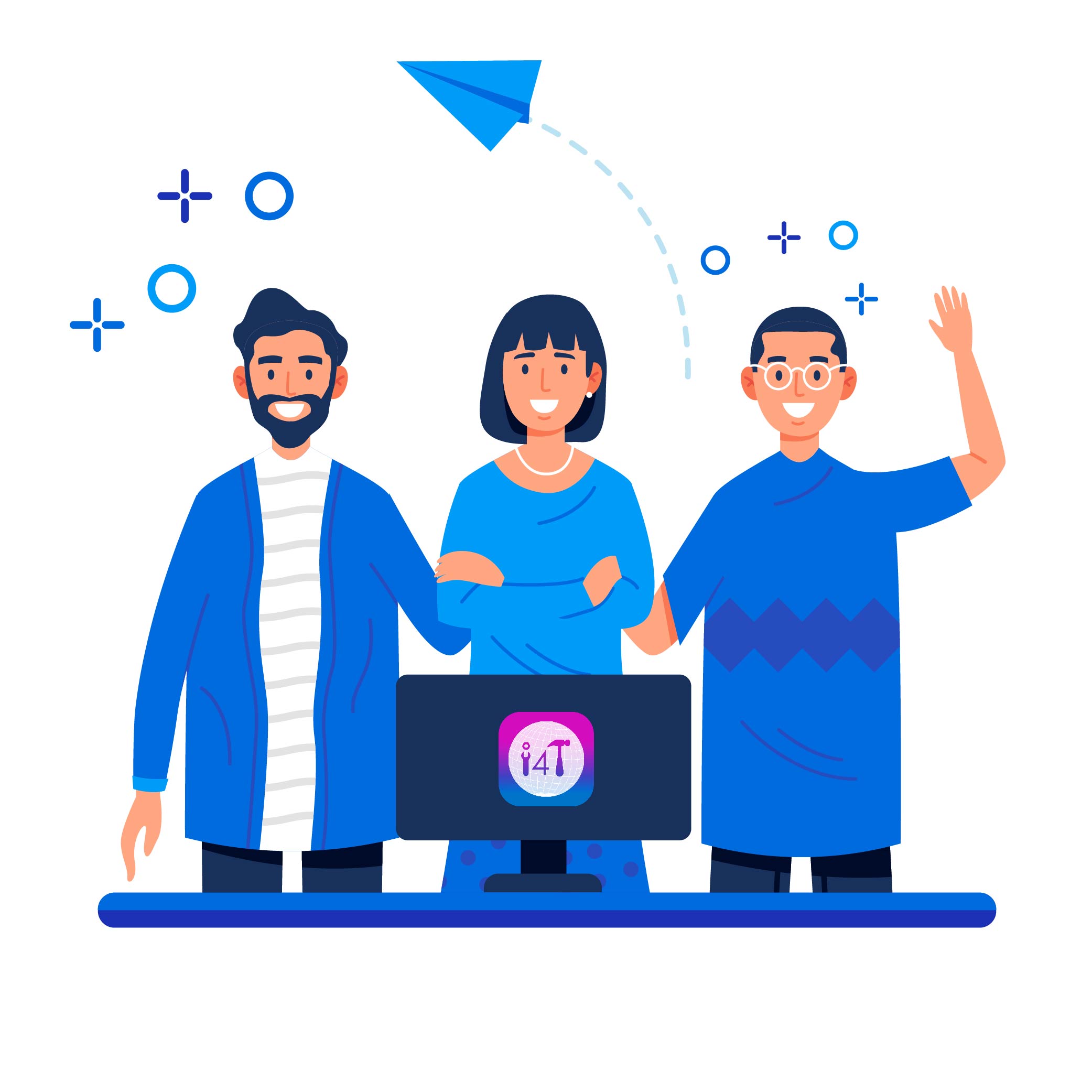
With our cutting-edge technology and in-depth knowledge of how the Field Service Management sector operates, the i4TGlobal Team loves to share industry insights to help streamline your business processes and generate new leads. We are driven by innovation and are passionate about delivering solutions that are transparent, compliant, efficient and safe for all stakeholders and across all touch points.